Thermal Insulation Properties of Low Thermal Conductivity Magnesium-Aluminum Spinel Bricks
The energy consumption of cement rotary kiln is very serious, especially when the refractory materials in the transition zone before and after the cement rotary kiln are not protected by the kiln skin, the refractory bricks are directly affected by material erosion, heat load and mechanical stress, and the use conditions are very harsh. At present, the transition zone of large cement rotary kilns generally uses Silicon carbide mullite bricks, silica-molybdenum red bricks or magnesia-alumina spinel bricks, and the service life basically meets the requirements of cement production. However, due to the large thermal conductivity of magnesia-alumina spinel bricks and silica-molybdenum bricks, Silicon carbide mullite red bricks, magnesia-alumina spinel bricks ≥3.0 W/m·K, Silicon carbide mullite bricks ≥2.8 W/m·K. As a result, the outer wall temperature of the cylinder in the transition zone before and after the operation of the cement rotary kiln is too high, averaging about 340℃ and up to 400℃. The higher outer wall temperature of the cylinder brings a series of problems, such as increasing the coal consumption per ton of cement clinker and increasing the emission of polluting gases. Severe cases also cause “red kilns”, affecting the safe operation of cement rotary kilns.
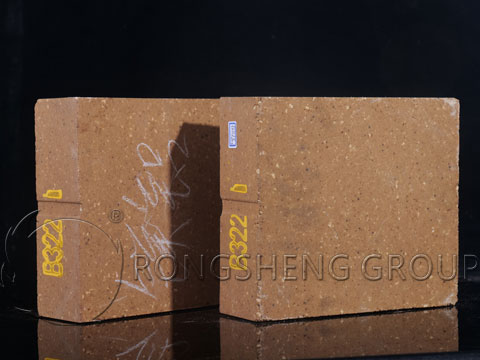
Low Thermal Conductivity Magnesia-Alumina Spinel Bricks
In order to solve the problem of high thermal conductivity of magnesia-alumina spinel bricks, the sintering performance and microstructure of rare earth oxide-doped porous magnesia-alumina spinel refractory aggregates were studied. Porous magnesia-alumina spinel was prepared with industrial α-alumina micropowder and fused magnesia sand as the main raw materials, sodium dodecylbenzene sulfonate (SDBS) as the foaming agent, and dextrin as the binder. In addition, different mass fractions of Y2O3, Yb2O3, La2O3, and Sm2O3 were added respectively, and the samples were kept warm for 3 hours at 1600℃ for sintering. The bulk density and apparent porosity of the sintered samples were measured respectively, and the phase composition and microstructure were analyzed by XRD, SEM, EDS, and other characterization methods to reveal the mechanism of rare earth oxides promoting the sintering reaction process of porous magnesia-alumina spinel.
The introduction of rare earth oxides promotes the sintering of magnesium-aluminum spinel. The sample volume density and compressive strength reach the maximum when the Sm3O2 addition is 1.5wt%, which are 2.28g/cm³ and 50.5Mpa, respectively. A substitution solid solution is formed between the rare earth oxides and magnesium-aluminum spinel, which promotes the sintering densification of magnesium-aluminum spinel. Cation vacancies and lattice defects of magnesium-aluminum spinel are conducive to the development and growth of magnesium-aluminum spinel crystals. The thermal conductivity of the product made from this raw material is significantly lower than that of similar products.
The lightweighting of refractory materials is mainly achieved by introducing a certain amount of pores into the materials, which has a lower thermal conductivity without significantly reducing the strength of the refractory materials. It can save energy and reduce resource consumption in the preparation and service of raw materials, which is a direction of research and development of refractory materials. Therefore, the development of new low thermal conductivity magnesium-aluminum spinel lightweight refractory materials has important practical significance for energy saving and consumption reduction in the cement industry.
When synthesizing magnesium-aluminum spinel lightweight aggregate, adding yttrium oxide, ytterbium oxide, lanthanum oxide and samarium oxide can increase the volume density of the sample, reduce the apparent porosity, increase the compressive strength, and promote the formation of magnesium-aluminum spinel. Among them, the sample with samarium oxide added has better sintering performance. When the addition amount of Sm2O3 reaches 1.5 wt%, the sample has the lowest apparent porosity and the highest volume density of 2.28g/cm³ and 31.72%, respectively.
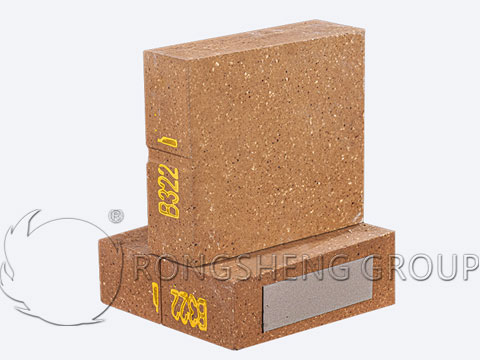
Application of Low Thermal Conductivity Magnesia-Alumina Spinel Bricks
The low thermal conductivity multi-layer composite magnesia-alumina spinel bricks developed by the above technology are used in 24-32 meters, and the average temperature is 43℃ lower than that of magnesia-alumina spinel bricks, and the service life reaches more than 12 months. Low thermal conductivity magnesia-alumina spinel bricks are not only recognized by domestic customers, but also have been used in many rotary kilns by overseas customers such as Mexican cement and Turkey, and have been highly praised.
In response to the high energy consumption and high carbon emissions in the cement industry, the low thermal conductivity multi-layer composite magnesia-alumina spinel bricks studied by Rongsheng Refractory Material Factory have the following advanced features: through the form of a three-layer composite structure, the working layer is optimized, the thermal conductivity of the working layer is reduced, the thermal shock resistance is improved, and the insulation layer is optimized to improve the strength of the insulation layer. Through the study of different insulation materials, zirconia reinforced alumina fiberboard with excellent high temperature resistance is selected as the insulation layer material. In the preparation process, innovative production processes are used to achieve synchronous molding and synchronous firing, simplify the process, reduce costs, and improve production efficiency. The thermal conductivity of low thermal conductivity magnesium-aluminum spinel brick is 2.4-2.5W/(m·K), which is much lower than the 3.0-3.3W/(m·K) of ordinary magnesium-aluminum spinel brick.
According to the actual application feedback from customers, low thermal conductivity multi-layer composite magnesium-aluminum spinel brick can effectively reduce the temperature of the transition zone cylinder of cement kiln, with significant energy saving and carbon reduction benefits. It provides a new direction for energy saving and emission reduction of cement rotary kiln.
Magnesium-Aluminum Spinel Brick for Lime Kiln
Magnesium-aluminum spinel brick for lime kiln is a high-performance refractory material designed for lime kiln. It is mainly composed of magnesium-aluminum spinel (MgAl2O4) generated by the reaction of magnesium and aluminum oxides at high temperature, and may contain a certain amount of other refractory oxides to enhance its performance. Magnesium-aluminum spinel has excellent high temperature resistance, corrosion resistance, thermal shock resistance and other characteristics, making it an ideal choice for key parts in lime kiln (such as burning zone, preheating zone, etc.).
Magnesium-aluminum spinel bricks for lime kilns have the following characteristics:
(1) High temperature resistance: Magnesium-aluminum spinel bricks have extremely high refractoriness and can withstand the high temperature environment in the lime kiln, ensuring the stable operation of the kiln.
(2) Corrosion resistance: In the reducing atmosphere of the lime kiln, magnesium-aluminum spinel bricks can resist the erosion of kiln slag and furnace gas, extending the service life.
(3) Thermal shock resistance: Magnesium-aluminum spinel bricks have good thermal shock resistance and can withstand the thermal stress caused by the rapid change of kiln temperature, preventing the brick body from cracking and falling off.
Magnesium-aluminum spinel bricks are mainly used in key areas such as the firing zone and preheating zone of the lime kiln. These areas have extremely high requirements for the performance of refractory materials. The use of magnesium-aluminum spinel bricks can significantly improve the operating efficiency and product quality of the lime kiln. Contact Rongsheng manufacturers for free samples and quotations.