Honeycomb ceramic is a kind of porous industrial ceramic, whose internal shape is many parallel channels in honeycomb shape. These honeycomb units are divided into lattice-like thin partition walls. Compared with general block ceramics, honeycomb ceramics have the characteristics of large specific surface area, low-pressure drop, low resistance, high-temperature resistance, good chemical stability, low thermal expansion, good thermal insulation, lightweight, and high strength. Therefore, it is particularly suitable for catalyst carriers for various purposes. In addition, since the fluid can pass through the cavities on the upper and lower surfaces of the honeycomb ceramic partitions, the honeycomb ceramic partitions can be used for heat exchange and chemical reactions. At present, honeycomb ceramics are widely used in kiln regenerators, automobile exhaust purifiers, and ozone suppression catalyst carriers. Heat exchange and filtration of molten metal in the metallurgical industry, chemical reaction carriers and catalysts in the chemical industry, and purification of toxic gases and liquids in the mining industry. Spraying in the light industry as well as sound-absorbing materials in the building materials industry and heat insulation materials for kilns.
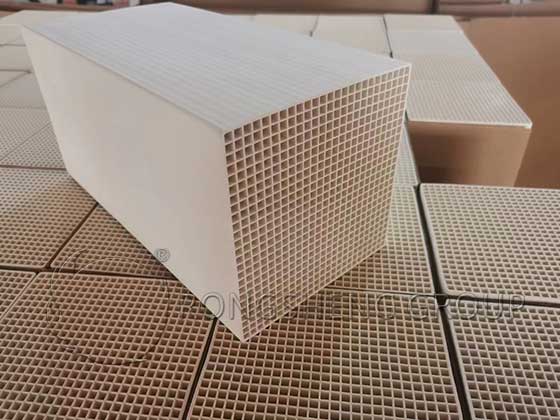
Honeycomb ceramics can be made from a variety of materials. The main materials are cordierite, mullite, aluminum titanate, silicon carbide, zirconia, silicon nitride, cordierite-mullite, cordierite-aluminum titanate, and other composite matrices.
Cordierite Honeycomb Ceramic Heat Storage Material
Cordierite has been widely used due to its good compatibility with various catalysts, large specific surface area, small thermal expansion coefficient, and good thermal shock resistance. Cordierite (2MgO·2Al2O3·5SiO2) honeycomb ceramics were prepared using clay, talc, and alumina, which have the advantages of low thermal expansion coefficient and high porosity. Although cordierite has many advantages, it still has disadvantages. That is, the heat resistance is slightly poor, so many subsequent studies will focus on adding other materials to cordierite to improve the performance of cordierite. Adding some additives to cordierite can promote the sintering of cordierite, reduce the thermal expansion coefficient, and improve thermal shock resistance. Common additives include sillimanite, silicon carbide, zirconia, germanium oxide, lithium carbonate, and calcium fluoride. In addition, it is sintered to form complex phase materials such as sillimanite-cordierite, mullite-cordierite, aluminum titanate-cordierite, spinel-cordierite, etc.
The raw material formula is 40% ~ 70% cordierite, 5% ~ 15% sillimanite, 10% ~ 20% andalusite, and 15% ~ 35% zircon by weight. Regenerative ceramic balls and honeycomb bodies were prepared. After testing, 90% of the samples were able to withstand more than 35 thermal shocks and were qualified products. And the sample performance is better than that of alumina ceramic balls. Silicon carbide-cordierite porous ceramics were prepared. The test results show that compared with silicon carbide porous ceramics, the flexural strength of silicon carbide-cordierite porous ceramics is significantly improved and the thermal expansion coefficient is significantly reduced. However, the apparent porosity decreased. The ways to reduce the thermal expansion of honeycomb cordierite ceramic materials are described from several aspects such as adjusting reasonable chemical composition, adding different amounts and types of additives, and improving the firing process. Moreover, beneficial effects have been achieved in the above-mentioned ways.
GeO2 was used to replace SiO2 in cordierite, and the variation of the thermal expansion coefficient of MgO·2Al2O3 ·(5 – x) SiO2 ·xGeO2 with the addition of GeO2 was studied. When x≤1, the thermal expansion coefficient decreases overall. Zirconia is introduced into cordierite to achieve toughening and strengthening purposes. Phosphate and lithium aluminum silicate are introduced into cordierite to lower the sintering temperature, increase density, and reduce the thermal expansion coefficient.
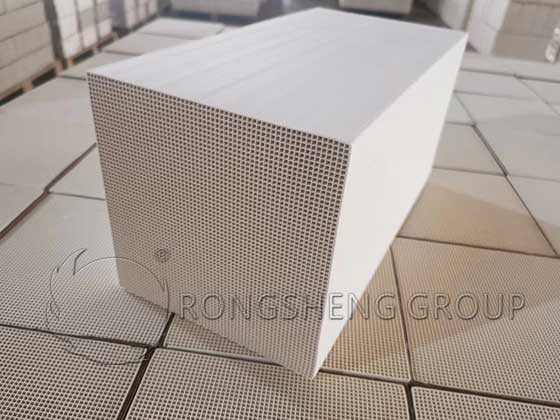
Application of Cordierite Honeycomb Ceramics
Cordierite honeycomb ceramics have been successfully used in many fields. This article mainly explains its application in controlling air pollution, honeycomb ceramic regenerators, and setting plates.
control air pollution
In recent years, with the rapid development of the economy, environmental pollution caused by the transportation industry has become increasingly serious. Problems such as haze weather and PM2.5 pollution are becoming more and more prominent. For human health, people have developed a variety of purification technologies. Cordierite honeycomb ceramics have the advantages of a large specific surface area, good thermal stability, and a small thermal expansion coefficient. It has been widely used in automobile exhaust emission treatment and removal of NOx and SO3 in industrial flue gas. The application of honeycomb ceramics and foam ceramics in extreme environments such as high temperatures and strong corrosion. Cordierite honeycomb ceramic materials have high thermal stability and chemical stability. Using it as a catalyst carrier plays a key role in purifying automobile exhaust and reducing nitrogen oxide emissions from power plants. Cordierite honeycomb ceramic is an important carrier in the catalytic treatment of automobile exhaust gas.
Honeycomb Ceramic Regenerator
Regenerative high-temperature air combustion technology (High-Temperature Air Combustion) is a revolutionary new combustion technology. It uses efficient heat storage materials to preheat combustion air from room temperature to an unprecedented temperature of 800°C. At the same time, nitrogen oxide emissions are greatly reduced and the exhaust gas temperature is controlled within the range between above the dew point and below 150°C. Maximize the recovery of flue gas waste heat and make the combustion temperature in the furnace more uniform. This technology is hailed as one of the most promising technologies in the 21st century. One of the keys to this technology is the preparation of high-performance regenerator materials—honeycomb ceramics. Cordierite honeycomb ceramic regenerator has significant advantages such as high-temperature resistance, corrosion resistance, good thermal shock stability, high strength, large heat storage, and good thermal conductivity. Energy saving effect and service life are greatly improved.
Setting board
Because cordierite honeycomb ceramics have the characteristics of light weight, fast heat conduction, and good thermal stability. It is used as a powder metallurgy setter to replace alumina setters. In addition, honeycomb ceramics are also used as sintered setters for denture production. Generally, a denture sintering furnace needs to complete a rapid temperature rise process from room temperature to 900°C within 2 to 3 minutes. This requires that the burner plate in the furnace have high thermal shock resistance and will not be damaged by rapid temperature rise in a short period. The low thermal expansion coefficient of cordierite honeycomb ceramics can well meet this requirement.
As the performance of cordierite honeycomb ceramics improves, its applications are becoming more and more widespread. The demand for honeycomb ceramics in the field of environmental protection will be increasing in the future. We must also pay attention to research in this area in the future to make the performance of domestic cordierite honeycomb ceramics better and better. To purchase high-quality cordierite honeycomb ceramic products, please contact us.