In RS refractory manufacturers, there are various types of refractory ramming materials. Aluminum-mullite ramming material, high alumina (or corundum)-silicon carbide-carbon ramming material, partial alkali fire ramming material, and zirconium corundum ramming material, etc. Among them, silicon carbide ramming material is mainly used as a coreless induction furnace lining for melting and heat preservation of iron, steel, and non-ferrous metals. Silicon carbide ramming material is a good choice for kiln linings that require high temperature and wear resistance. Due to the continuous upgrading of high-temperature furnace lining requirements for refractory materials, Al2O3-SiC-C Refractory Ramming Mass ramming materials are gradually being used.
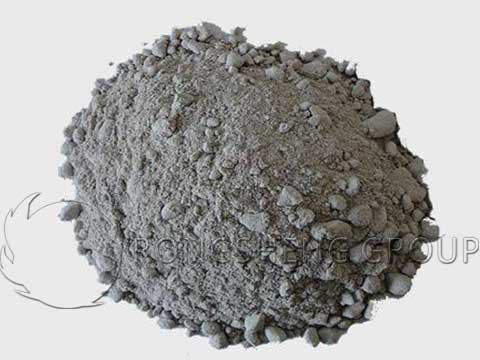
Advantages of Using Refractory Ramming Material in High-Temperature Furnace Lining
As we all know, refractory ramming material is composed of refractory aggregate, granular material, binder, and water reducer in proportion, and is constructed by ramming, so it is called refractory ramming material. Classification of refractory ramming materials. According to the type of refractory aggregate, it is divided into clay, high alumina, zirconium corundum, silicon, mullite, and silicon carbide. According to the type of binder, it is divided into sodium silicate, sodium sulfate and polyphosphate, aluminum sulfate, marinade, concrete, fusion clay, and organic chemical binder, etc. All in all, except for raw materials with special functions such as refractory mud, all unshaped refractory insulation materials can be constructed by ramming only by reducing the water demand or chemical binder usage by 1/3~1/2. And their performance is also improved.
The high-temperature kiln lining constructed with refractory ramming materials has low water content, compactness, and better characteristics than castables of the same material. The main disadvantage of refractory ramming material is that the construction speed is relatively slow, and the labor intensity in the construction is high, which is also the factor that it is replaced by vibration material and high-quality castable.
Refractory ramming materials are widely used, especially in industrial furnaces such as melting furnaces, and more will be used. In recent years, on the basis of silicon carbide refractory ramming materials, refractory manufacturers have also developed a variety of carbon and silicon carbide refractory ramming materials. Its application in the lining of blast furnace iron troughs has a certain improvement in the service life of traditional iron trough lining. In places such as crossing rivers of various warm-weather iron furnaces, zirconium-containing aluminum-carbon fireproof ramming materials are used to cast working linings, and good results have also been obtained. Raw materials with excellent properties such as silicon carbide and Si3N4 refractory ramming materials have also been used in ironmaking blast furnaces.
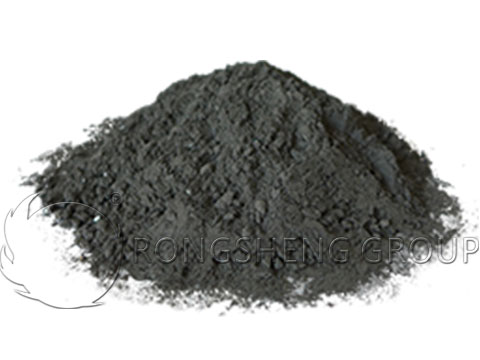
Silicon Carbide Ramming Mass
Silicon carbide ramming material is a mixture made of quartz as the main raw material and a small amount of sintering agent. Sintering agent compounds include boric acid, alkali metal borates, alkali metal phosphates, alkali metal silicates, and the like. These compounds have the effect of promoting sintering at medium and low temperatures. Silicon carbide ramming material has the characteristics of stable chemical properties, high-temperature resistance, wear resistance, erosion resistance, and corrosion resistance. Silicon carbide has high thermal conductivity, 64.4W/(m·K) at 500°C, and can transfer heat quickly.
Silicon carbide ramming material is made of high-purity, large-grain silicon carbide, corundum, chrome corundum superfine powder, aluminum chromium phosphate binder, and admixtures under specific conditions. It is an air-hardening ramming material, which can be solidified in the air. Its strength is formed because the colloidal binder is dehydrated and concentrated at a temperature of 35°C to 240°C, polymerized, and chemically combined with silicon carbide, corundum, and micro-powder.
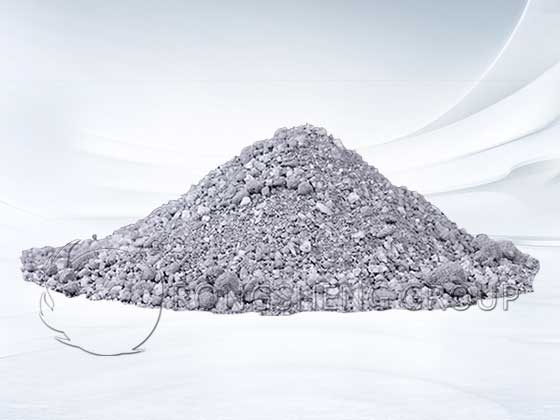
Al2O3-SiC-C Refractory Ramming Mass Material
Al2O3-SiC-C Refractory Ramming Mass material is a mixture composed of high-alumina clinker, silicon carbide, carbon material, binder, and admixture, which is constructed by the ramming method. High-Alumina Silicon-Carbide Carbon Refractory Ramming Mass material is mainly used in the tapping trough and slag ditch lining of medium and small blast furnaces.
Generally, the high bauxite clinker for preparing this type of ramming material requires that the content of impurities (Fe2O3, R2O) be as low as possible, and the water absorption rate is less than 4.5%. Its particle size composition is 40%-60% of coarse particles (8-2 mm), 10%-20% of medium particles (2-0.074 mm), and 30%-40% of fine particles (less than 0.074 mm). The silicon carbide is black silicon carbide with a particle size of less than 100 mesh. The carbon material can be metallurgical coke or graphite, which requires low impurity content and high fixed carbon content. RS refractory manufacturers propose that soft clay or bentonite can also be added in order to improve the operational performance of the ramming material and the sintering performance in use. Depending on the temperature used, sintering aids at different temperatures can also be added.
Binders for this type of ramming material, Al2O3-SiC-C Refractory Ramming Mass, include asphalt, tar (anthracene oil) + asphalt, liquid phenolic resin, aluminum dihydrogen phosphate, etc. When asphalt is used as a binder, water should be added to mix the ramming material, and it should be baked before use after ramming. When tar (or anthracene oil) + asphalt is used as the binder, there is no need to add water when preparing the ramming material, and the molten iron can be passed directly after ramming without baking, so as to avoid baking the ramming material. However, the flue gas in use is relatively large, which will pollute the environment. When the liquid phenolic resin is used as a binder, there is no need to add water, and it can be put into use directly without baking, and it is also a baking-free ramming material. The environmental pollution is light, but the storage period of the ramming material is short, so it is best to use it directly on-site. When aluminum dihydrogen phosphate is used as a binder, the corrosion resistance of molten iron and slag is poor, so it can only be used as the lining of a small blast furnace tapping trough, and aluminum tri-hydrogen phosphate is basically not used as a binder now.
The additives used to improve the performance of Al2O3-SiC-C Refractory Ramming Mass materials include antioxidants, plasticizers, sizing agents, anti-shrinkage agents, etc. The purpose of adding antioxidants is to prevent excessive oxidation of carbon materials, and metal silicon powder and metal aluminum powder are usually used as antioxidants. Plasticizers generally use plastic clay. The purpose of adding a wetting agent is to make silicon carbide, carbon materials, and oxide refractory materials well mixed together. The anti-shrinkage agent is added to prevent cracks in the ditch lining due to excessive shrinkage during use. Generally, fine silica particles can be used as an anti-shrinkage agent.
At present, the high-alumina silicon-carbide carbon ramming mass material used in the tapping trough of medium and small blast furnaces has gradually changed from the type that needs to be baked to the type that does not need to be baked. The advantage of non-baking ramming material is that it can save the time of ditch repairing, and it can also avoid excessive oxidation of carbon materials during the baking process, which will reduce the resistance to slag penetration and erosion of the ditch lining.
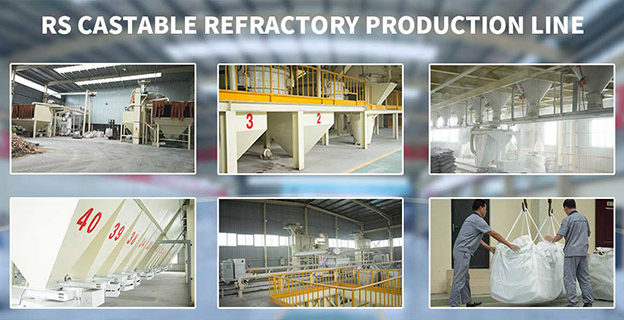
Rongsheng Refractory Material Manufacturer
Rongsheng refractory manufacturers mainly provide refractory lining materials for industrial high-temperature kilns, including various types of refractory brick products and unshaped refractory products. Our refractory materials include various refractory materials for high-temperature industrial kiln maintenance and refractory materials for heat preservation. Our excellent technical team can also provide the design of refractory lining materials, the design of refractory materials for the insulation layer, and other solutions for refractory lining materials. Of course, our experienced refractory construction team also provides the construction of various industrial kiln refractory linings. Contact us for free refractory solutions for high-temperature industrial kilns. More opportunities to get free refractory samples for trial use.