Introduction to the Refractories Setter Plate. The Setter Plate is a protective material used in high-temperature situations. It is mainly used for the construction and maintenance of the linings of various furnace drums, furnace linings, reactors, electric furnaces, and other industrial equipment. The Setter Plate can withstand high temperatures and has the characteristics of fire prevention, acid and alkali resistance, and heat preservation. It is one of the indispensable materials in industrial production.
When the Setter Plate is in service, it must withstand the thrust during movement and the friction when loading and unloading products, and it will not crack when used in hot and cold cycles. Under the condition that the thermal shock resistance of the Refractories Setter Plate is satisfied, improving the bending resistance and crack resistance of the Setter Plate is the key. The material of the setter plate is required to be extremely chemically inert and not react with the products being burned. The material of the Setter Plate is divided into alumina, zirconia, composite, etc. Mainly used in electronic ceramics, special ceramics, and other fields.
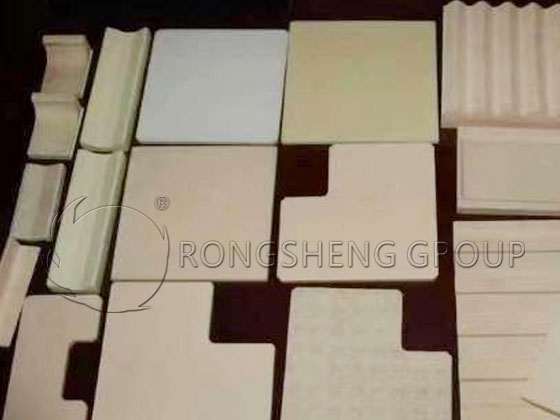
Types of Setter Plates
- Ceramic Setter Plate
Ceramic setters are a common type of setters. Its main raw materials are high-purity siliceous rocks and alumina. The advantage of ceramic setters is that they have high mechanical strength and chemical stability, and can be used in high temperatures and acid-base environments for a long time.
- Refractory Brick Setter Plate
Refractory bricks are made of refractory materials that have been sintered at high temperatures. It has good high temperature resistance and is usually used to make refractory brick furnace drums, refractory brick furnace linings, etc.
- High Aluminum Setter Plate
The main component of high-aluminum setters is alumina, which has good high-temperature stability. It is usually used in high-temperature furnace linings in metallurgy, chemical and other industries.
- Silicate Fiber Setter Plate
Silicate fiber setter plate is a new type of setter plate made of silicate fiber. It has the advantages of lightweight, good thermal insulation performance, and high-temperature resistance. It is a setter plate widely used in industrial production.

Refractories Setter Plates
Cordierite Mullite Plate Kiln Furniture 1370 ℃
Cordierite mullite plate kiln furniture uses selected mullite and cordierite as the main raw materials. Advanced production technology, specializing in the manufacture of high-end kiln tools such as burner plates, shed plates, saggers, flame baffles, slide rails, backing plates, Setter Plates, pillars, etc. for kilns such as ceramics and powder metallurgy. Its refractoriness is higher than cordierite, and its thermal stability is better than mullite corundum material. It has small thermal expansion coefficient, good thermal shock stability, long service life and no sudden breakage. It will not oxidize, get dirty or slag, or contaminate ceramic products during use.
Mullite-cordierite kiln furniture is an ideal material for firing ceramic products below 1300°C. Excellent results have been achieved in the firing of daily ceramics, sanitary ceramics, display ceramics, glazed mosaics, Western bricks, square bricks, split bricks and glass-ceramics. It can be used in tunnel kilns, shuttle kilns, mesh belt furnaces, push rod furnaces, etc. for low-temperature bisque firing, glaze firing or powder metallurgy heat treatment of daily ceramics.
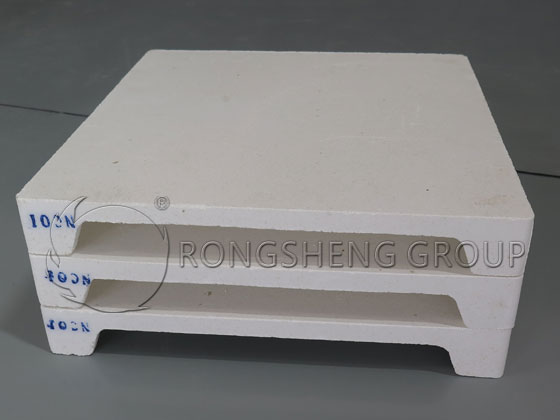
Silicon Carbide Sandwich Panel
Silicon carbide sandwich panels are suitable for magnetic materials, high-temperature resistant sandwich panels, high-strength sandwich panels, and calcined honeycomb sandwich panels.
Introduction to product characteristics and advantages of silicon carbide sandwich panels
Sandwich shed board and silicon carbide sandwich setter plate are a new composite product made of silicon carbide, alumina and zirconia and sintered at high temperature. Advantages: It has excellent thermal conductivity and high-temperature load performance of silicon carbide. Product characteristics of high-purity silicon carbide Sandwich boards, silicon carbide Sandwich boards, corundum sandwich panels, corundum silicon carbide sandwich setter plates, silicon carbide push plates, shed boards and setter boards:
- (1) The product is resistant to deformation at high temperatures and does not need to be turned over for long-term use. It can significantly improve the firing quality of ceramic products and reduce the labor intensity of operators.
- (2) The surface of the shed board is smooth, there is no slag during use, and the service life is long, which is more than three times the normal service life of similar domestic silicon carbide shed boards.
- (3) It has good resistance to rapid cooling and heating, the temperature rise and fall does not exceed 300℃ per hour, and there is no cracking in the shed board.
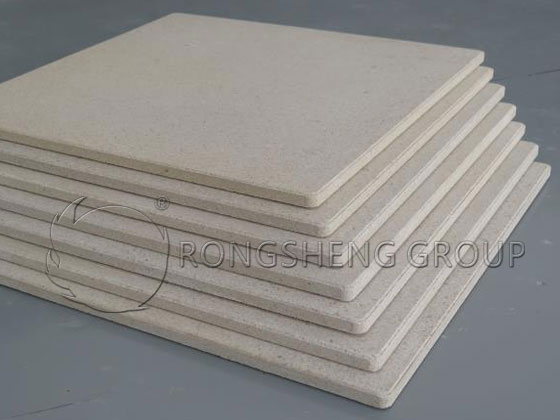
Advantages of High Purity Silicon Carbide Sandwich Plate
High-purity silicon carbide Sandwich setter plate has excellent thermal conductivity and high temperature load performance of silicon carbide. At the same time, the alumina and zirconia surface layers can effectively ensure that the shed panels will not react with the product when used at high temperatures. Suitable for use in various electronic component sintering kilns.
Common specifications: (mm)
295*295*11 310*310*11 320*320*11 320*150*11 300*300*11
[Note: Thickness can be produced according to customer requirements]
Corundum Burning Plate
Corundum Setter Plate refers to high-end kiln furniture whose main crystal phase is α-Al2O3. It has excellent properties such as high strength, corrosion resistance, high-temperature resistance and wear resistance. High temperature (>1650℃) has small deformation, but the sintering temperature is high and the thermal shock stability is poor. During the firing process of lead zirconate titanate piezoelectric ceramics, the corundum setter plate faces central warping, surface layered powdering and peeling.
Zirconia Setter
Zirconia is a corrosion-resistant, high-temperature resistant refractory oxide. Zirconia setters are often used as sintering Setter Plates for dielectric ceramics, powder metallurgy, chip capacitors, ferrite magnetic materials and other products. The zirconia setter plate is used to prevent adhesion of parts during sintering and the loss of electromagnetic properties of electronic components.
The firing temperature of conductive ceramics, device porcelain, etc. is generally between 1400 and 1650°C, and they are generally corundum-mullite, corundum, or composite.
Barium titanate ceramics are star products in the electronic ceramics industry. Sintering is an important step in its preparation process and is the final stage that determines the densification and microstructure of barium titanate. Therefore, the quality of the setting plate is particularly important. Due to its low melting point (1625°C) and high density, barium titanate is alkaline. Traditional aluminum-silicon kiln furniture is easy to react with it, causing contamination of the products. Relevant foreign kiln furniture manufacturers apply plasma spraying technology to the preparation process of setters. That is, the middle layer of the setter plate is made of corundum-mullite material and the outer layer is made of zirconia deposited coating. It has high thermal shock resistance and does not react or stick to fired chip laminated ceramic capacitors.
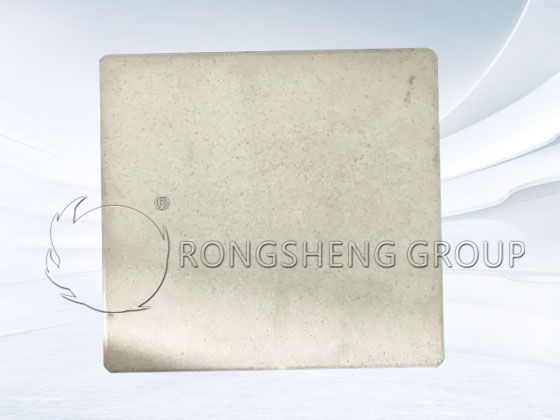
Thermal Shock Resistance of Corundum-Mullite Setter Plate
Corundum-mullite materials have high thermal shock resistance and high temperature strength, and have good chemical stability and wear resistance. Therefore, it can be used repeatedly at higher temperatures (1450°C) 100 to 200 times. Especially suitable for sintered magnetic cores, ceramic capacitors and insulating ceramics.
At present, most domestic capacitor manufacturers use corundum-mullite setters. Among them, setters with higher requirements are often expensive. Domestic corundum-mullite Setter Plates have a low service life and poor stability. Mainly due to its poor thermal shock stability, it is easy to break during use. The thermal stability of Setter Plate products is mainly determined by the corundum-mullite matrix. Therefore, it is of high practical significance to conduct research on the thermal shock stability of corundum-mullite composite materials.
The burning product is a laminated burning product. The weight of each layer of Setter Plates plus the product is about 1kg, and is usually stacked in about 10 layers. Therefore, the setter plate may withstand a maximum pressure of more than ten kilograms. At the same time, it has to withstand the thrust when moving and the friction when loading and unloading products, as well as multiple hot and cold cycles, making the use environment very harsh.
Through experiments with high-quality raw materials, it can be concluded that regardless of the interaction of the three factors, alumina powder, kaolin and calcination temperature have an impact on thermal shock resistance and creep. Under experimental conditions, the thermal shock resistance increases with the addition of alumina. Decreases as the firing temperature increases. It is the lowest when the kaolin content is 8%, followed by the kaolin content of 9.5%. The amount of creep decreases with the addition of alumina powder, and is the lowest when the kaolin content is 8%. The creep amount is maximum when the calcination temperature is 1580℃. Taking into account the thermal shock resistance and creep amount of the material, the best effect is achieved when the alumina content is 26%, kaolin is 6.5%, and the calcination temperature is 1580°C.
There is a certain gap between the corundum-mullite particles and the matrix. There are some cracks around the particles. This is caused by the mismatch in thermal expansion coefficient and elastic modulus between the particles and the matrix, causing micro-cracks in the product. When the expansion coefficients of particles and matrix do not match, the aggregate and matrix tend to separate when heated or cooled. A clearance layer is produced in the middle, causing microcracks to appear. The existence of these microcracks will lead to a decrease in the mechanical properties of the material, but when the material is subjected to thermal shock. It can also act as a “buffer zone” in the gap between aggregate and matrix, absorbing certain stress. Avoid stress concentration at the crack tip. At the same time, the thermal shock cracks generated in the matrix will first terminate at the gap between the particles and the matrix, which prevents crack expansion. This improves the thermal shock resistance of the material.
By creating enough cracks, and the cracks propagate in a quasi-static manner. It can improve the resistance of products to catastrophic crack growth. It can stop the cracks that have formed on the particle surface or extend the path of the cracks along the particle surface. Microcracks prevent the material from dynamic crack propagation. The content of alumina powder and kaolin and the firing temperature will have a great impact on the bonding state and cracks between the particles and the matrix, thus changing the thermal shock resistance of the material.
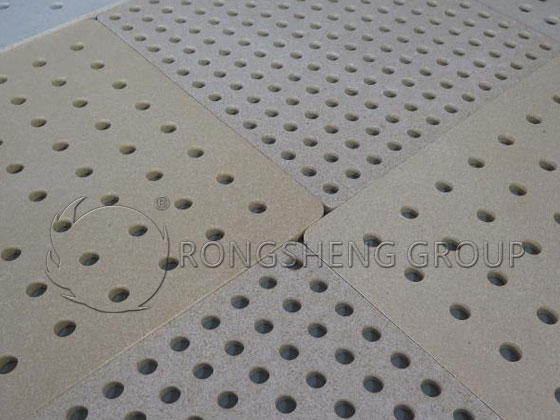
How to Choose a Setter Plate
- Choose the appropriate type of Setter Plate. According to the needs of industrial production, select the corresponding setter type.
- Carry out corresponding processing and installation according to the shape and size of the equipment lining. Templates can usually be used to process and cut the setters into appropriate shapes and sizes for installation.
- Use appropriate adhesive to stick the Setter Plate on the inner wall of the equipment to ensure reliable fixation.
In short, the setter plate is a very important industrial material. It is widely used in the construction and maintenance of high-temperature equipment such as furnace drums, furnace linings, reactors, and electric furnaces. When using, the appropriate type of Setter Plate should be selected according to specific needs. Proper installation and use can ensure the normal operation and service life of the equipment.