According to the daily use habits of customers and refractory manufacturers, and the chemical mineral composition of refractory bricks. Refractory bricks can be roughly classified into silica-alumina series refractory bricks, basic refractory bricks, corundum bricks, carbon bricks(blocks), chrome bricks, and other types of refractory bricks. Learn more about the classification of fire bricks, Rongsheng refractory factory will help you and provide you with high-quality refractory bricks and competitive prices. Next, Rongsheng refractory manufacturer will take you to learn more about the types of refractory bricks listed above.
1. Silica & Alumina Series Refractory Bricks
(1) Silica Bricks
Silica brick, the refractory brick containing SiO2 of more than 93%, is the main variety of acid-resistant brick. It is mainly used for masonry coke oven, also used in glass, ceramic, and carbon calciner, the arches of refractory brick and other load-bearing parts are also used in high temperature bearing part of hot blast stove, but it is not suitable for used in thermal equipment below 600 DEG C and the thermal equipment with large temperature fluctuation.
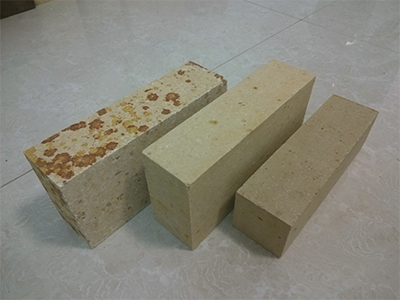
(2) Clay Bricks
Clay bricks are mainly composed of mullite (25% – 50%), glass phase (25% – 60%), and cristobalite and quartz (up to 30%). Usually, hard clay is used as raw material to pre-calcinate into mature materials, then mixed with soft clay to form semi-dry or plastic forming. The temperature is fired at 1300~1400 C to produce clay brick products. It is a firebrick commonly used in the blast furnace, hot blast furnace, heating furnace, power boiler, lime kiln, rotary kiln, ceramic, and refractory brick kiln.
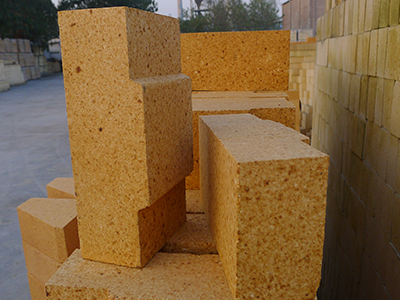
(3) High Alumina Refractory Brick
The mineral composition of high alumina firebrick is corundum, mullite, and glass phase. Its content depends on the ratio of AL2O3 to SiO2 and the type and quantity of impurities. It can be classified according to AL2O3 content.
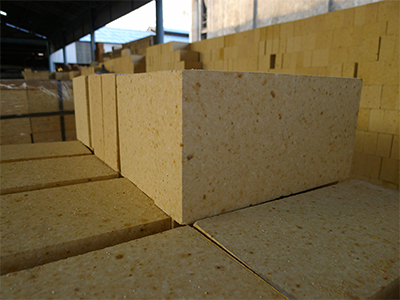
(4) Zirconium Corundum Brick
Zirconium corundum brick refers to a refractory product with a ZrO2 content of 33% to 45% using industrial alumina powder and selected zircon sand as raw materials. Zirconium corundum bricks are mainly used in glass industrial tank kilns. Zirconia corundum brick is also called fused brick, the English abbreviation is AZS. It is arranged in the order of the three chemical components of the Al2O3-ZrO2-SiO2 ternary system phase diagram according to their content. Al2O3 takes A, ZrO2 takes Z, SiO2 takes S, and national standards also use this abbreviation. For example, No. 33 fused cast zirconium corundum brick is abbreviated as AZS—33#, No. 36 fused cast zirconium corundum brick is abbreviated as AZS—36#, and No. 41 fused cast zirconium corundum brick is abbreviated as AZS—41#.
2. Corundum Refractory Bricks
Corundum refractory bricks refer to refractory brick products with alumina content greater than 90% and corundum as the main crystal phase. High compressive strength at room temperature, up to 340MPa. The high load softening start temperature is greater than 1700°C. Very good chemical stability, strong resistance to acidic or alkaline slag, metal, and glass liquid. Thermal shock stability is related to its organizational structure. Dense products have good corrosion resistance, but poor thermal shock stability. It can be divided into sintered corundum bricks and fused corundum bricks.
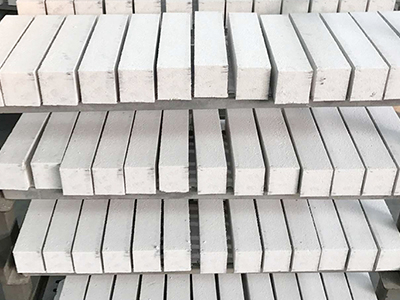
3. Carbon Refractory Bricks
Carbon bricks are made of coke, anthracite or graphite, and tar as raw materials, which are mixed, shaped and burned to 1450°C in a reducing flame to form a carbonaceous refractory. The mass fraction of carbon is 88% to 90%. It can withstand the erosion of molten metal and various slags but is easy to oxidize. Used for masonry bottom and belly of the blast furnace. It is also called carbon blocks.
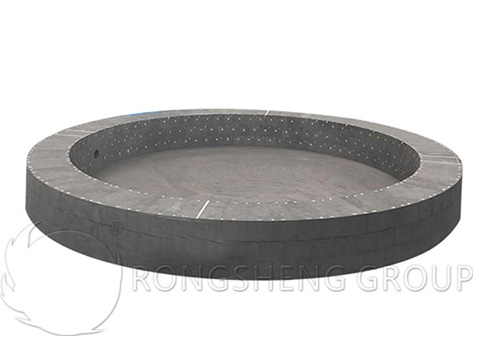
4. Chrome Bricks
Chrome brick is a refractory material made of chrome ore with a content of chromium trioxide greater than 30%. Chrome bricks are neutral bricks, which are weak in interaction with acidic and alkaline refractories at high temperatures, and their load softening temperature and thermal shock resistance are lower than magnesia chrome bricks. It is mainly used for the isolation layer of acidic and alkaline refractories at high temperatures, and also used for the lining of non-ferrous smelting furnaces, but it is not suitable for places where the atmosphere changes frequently in direct contact with molten iron. In order to improve the high-temperature performance of bricks, more than 10% magnesia is generally added to the material.
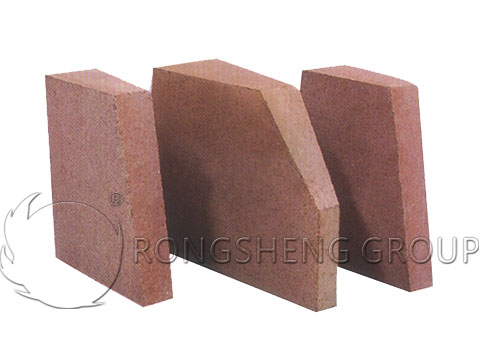
Chromium oxide bricks (also referred to as chrome bricks) were first used in non-ferrous metallurgical furnaces and gas slag furnaces. It has excellent resistance to corrosion of steel slag, non-ferrous smelting slag, coal gasification slag, and various glass liquids outside the furnace. In the past 10 years, this kind of refractory material has begun to be used in glass melting furnaces, but it is only limited to dark bottle glass melting furnaces or alkali-free glass fiber melting furnaces and is mainly used in high-temperature parts of glass melting furnaces. Such as the upper pool wall, small furnace mouth, liquid hole, charging port, etc. Because it can significantly extend the age of the kiln, it has attracted widespread attention in the glass industry.
5. Basic Refractory Bricks
Basic refractory bricks are refractories with basic oxides such as Mg0 and CaO as the main components. The main varieties are the following.
(1) Magnesite brick
Magnesite brick refers to the brucite as raw materials, the main crystalline is periclase, and the content of MgO is more than 80%~85%. Its products are divided into two major categories: Metallurgical magnesia and magnesia products. According to the chemical composition and different purposes, there is martin sand, ordinary metallurgical magnesia, magnesia silica brick, magnesia alumina brick, magnesia calcium brick, magnesia brick, and other varieties. The main product of magnesite brick is alkaline refractory brick, high refractoriness, has good resistance to alkaline slag, and iron slag, is a kind of important high refractory brick. Mainly used in the open-hearth furnaces, BOF, EAF, non-ferrous metal smelting, etc.
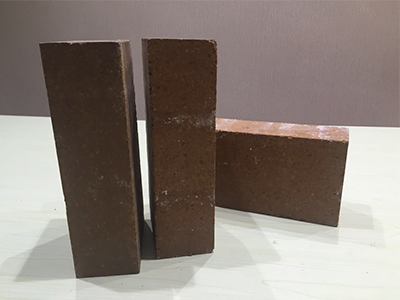
(2) Dolomite Brick
Dolomite brick is a kind of basic refractory with dolomite as the main raw material for production. It is widely used in the alkaline converter and can also be used as a lining for some outside refining ladles.
(3) Magnesia Alumina Brick
Magnesia alumina brick refers to an alkaline refractory made of magnesia and industrial lead oxide or alumina as raw materials, crushed, shaped, and fired at about 1600°C. The refractoriness is greater than 2000 ℃, the resistance to rapid cooling and heating is better than that of magnesia bricks, and it can resist the erosion of alkaline slag. It is used to build the furnace roof of steel-making alkaline open-hearth furnaces and electric furnaces.
(4). Forsterite Refractory Brick
the forsterite refractory brick is a refractory brick, mainly composed of 2MgO SiO2. Mainly used in open-hearth furnace regenerator, ingot brick, and heating furnaces, it also has a good effect used in the copper smelting furnace.
6. Other Types of Refractory Bricks
Of course, the types of refractory bricks are not limited to the few types that need to be listed. There are other types of refractory bricks, for example, some special refractory brick products, including pure oxide products, carbides, nitrides, silicides, cermets, etc. They came into being according to the special needs of some industrial kilns, and they are also an indispensable part of refractory brick materials. At the same time, in order to prevent the loss of heat, the contribution of refractory insulating bricks is indispensable in terms of energy-saving, heat preservation, and production cost saving.
Rongsheng Refractory Bricks Manufacturer
Each of these refractory bricks from the Rongsheng refractory factory has its own unique properties and characteristics. They previously complemented each other to escort the refractory lining of various thermal furnace equipment. Because the requirements of refractory linings in different parts of any kind of thermal furnace are different. Therefore, the refractory lining material of any thermal furnace cannot be built with only one kind of refractory brick, and different refractory bricks are required to be combined with each other.
To purchase various types of refractory brick products for industrial furnace lining, please contact the Rongsheng refractory material manufacturer. As the large refractory material manufacturers not only have high product quality but also provide good customer service and can have good customer service guarantees.