Refractories for Sponge Iron Production by Direct Reduction Method for Sale
The main products produced by the direct reduction method are solid sponge iron, iron granules, and liquid pig iron. Among them, the production method of sponge iron is the most mature and has the largest output. The production of sponge iron mainly uses iron concentrates, iron oxide scales, and other raw materials with high iron oxide content, which are reduced to metallic iron under the action of reducing media. The reaction is a solid-phase reaction and emits a lot of gas. There are many pores in the generated solid iron, like a sponge, so it is called sponge iron. The reaction temperature is generally between 800 and 1300°C. The reducing media used are mainly non-coke reducing agents such as coal, natural gas, and coal gas. The equipment used in the production of sponge iron by the direct reduction method mainly includes a shaft kiln, square kiln, annular kiln, rotary kiln, tunnel kiln, and continuous furnace at the bottom of the trolley, etc.
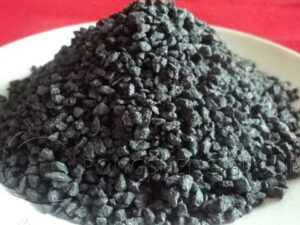
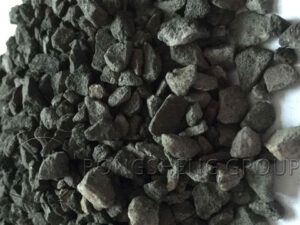
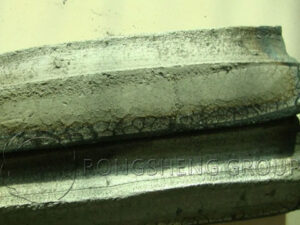
Production of Sponge Iron by Shaft Kiln
It uses natural gas and steam to produce reducing gas, and then reducing gas reduces iron ore into sponge iron in a shaft furnace. The production process of HYL III sponge iron can be divided into two parts, the gas-making boundary area, and the reduction boundary area. The gas production boundary includes the generation and purification of reducing gas. The reduction boundary includes heating of reducing gas and reduction of iron ore. In the gas production boundary zone, steam and natural gas are mixed and then catalytically cracked in the reformer to produce synthesis gas mainly composed of hydrogen and carbon monoxide, which is dehydrated and sent to the reduction boundary zone. The cracking reaction is:
CH4 + H2O = CO + 3H2
CO + H2O = CO 2 + H2
In the reduction boundary area, after dehydration and decarbonation of the shaft furnace top gas, it is mixed with the gas from the gas production boundary area to form a reduction gas and enters the reduction gas heating furnace together. The heated reducing gas enters the furnace from the bottom of the reduction section of the shaft furnace and flows from bottom to top. Iron ore is added from the top of the shaft furnace and moves from top to bottom. The reducing gas and iron ore undergo a chemical reaction in reverse motion to produce sponge iron. Among them, the chemical reactions that take place are:
3CO + Fe2O 3 = 2Fe + 3CO 2
3H2 + Fe2O 3 = 2Fe + 3H2O
Process for Producing Sponge Iron in Tunnel Kiln
A tunnel kiln is a modern continuous firing thermal equipment, which is widely used in the roasting production of medium sponge iron in the metallurgical industry. It can also be used in other industries such as refractory production. The reason why the tunnel kiln has a wide range of industrial applications is inseparable from its stable firing system.
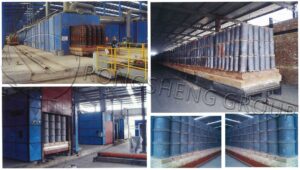
The tunnel kiln for firing sponge iron is a low-temperature kiln with a temperature range of 1000~1350℃. The heat source is clean energy natural gas, and the sponge iron reduction tank is transported by a kiln car for production reduction through a tunnel kiln. Tunnel kiln firing sponge iron is mainly divided into preheating zone, firing zone, and cooling zone. The temperature of these three parts can often be kept within a certain range. Therefore, the quality of the fired product is better.
Rotary Kiln for Producing Sponge Iron
The rotary kiln method, also known as the “SL/RN” method, uses solid fuel as a reducing agent and a rotary kiln as a reactor. The reducing agent and pellets (pig iron or pellets after oxidative roasting consolidation) simultaneously enter the rotary kiln for reduction roasting. The resulting sponge iron generally has a metallization degree of more than 90% and a particle size of 5 to 15 mm, which is usually used as a steelmaking raw material.
The working principle of the rotary kiln is to produce sponge iron. The raw material composed of solid carbon and ore particles (pellets) moves in the rotary kiln with the inclined furnace body and advances continuously. During the movement, the charge is preheated (<800°C region) and reduced (900-1000°C region) by the gas generated by the countercurrent or cocurrent combustion, and finally the product solid sponge iron is obtained.
Requirements for the Refractory Materials for Sponge Iron Production by direct reduction
At present, the sponge iron produced by shaft kilns with natural gas as the reducing medium in the world mainly accounts for about 80%. No matter what kind of kiln, the operating temperature is not high. Therefore, generally, aluminum-silicon-based refractories can meet the temperature requirements as kiln linings. However, it should be noted that Fe2O3 in the refractory material will be reduced to metallic iron and Fe3C under CO atmosphere conditions. The presence of Fe3C will promote the deposition of carbon, resulting in embrittlement cracking of the refractory. Therefore, in order to improve the service life of the furnace lining of the equipment, the Fe2O3 content in the refractory material should be reduced, and the structure of the selected material should be dense and the pores should be fine.
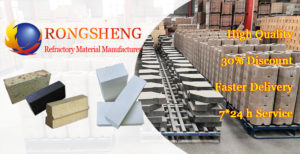
Rongsheng Refractory Manufacturer
Rongsheng is a refractory manufacturer with rich production and sales experience. Rongsheng’s refractory products have been sold to more than 70 countries around the world, such as South Africa, Philippines, Chile, Malaysia, Indonesia, Vietnam, Kuwait, Turkey, Zambia, Peru, Mexico, Qatar, Egypt, Russia, Kazakhstan, etc. . In solving the problem of refractory lining materials for industrial furnaces, we have also accumulated many cases and solutions for thermal furnaces of customers. If your thermal kiln needs refractory lining materials, please contact us to purchase refractory materials for the production of sponge iron kilns. It is best to attach the working conditions of your refractory kiln, the working environment of the refractory lining, the working temperature, erosion conditions, etc. Based on the information you provide, we will recommend the most suitable refractory for your production needs. In order to reduce the number of furnace shutdowns and repairs, improve production efficiency and increase production efficiency.