Manufacturer of Magnesia Alumina Spinel Bricks for Cement Kilns
Magnesia-alumina spinel bricks are made of high-purity magnesia sand and pre-synthesized magnesia-alumina spinel as the main raw materials and are made after reasonable grading, high-pressure molding, and high-temperature firing. Rongsheng is a manufacturer of magnesia-alumina spinel bricks for cement kilns. Magnesia-alumina spinel bricks are characterized by high purity, high strength, corrosion resistance, low linear expansion coefficient, and good thermal shock resistance. They are ideal refractory materials for the transition zone of cement rotary kilns.
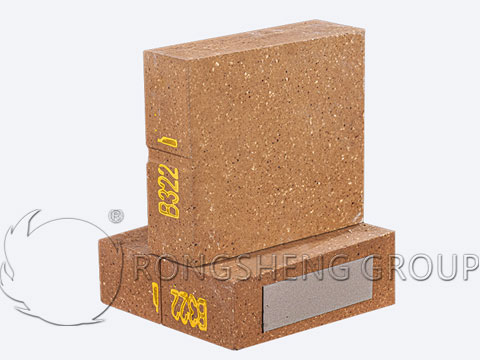
Production of Magnesium Aluminum Spinel Bricks
The amount of magnesium aluminate spinel added to the ingredients of magnesium aluminate spinel brick production is not the more the better. With the increase of spinel amount, the thermal shock resistance becomes better. However, due to mismatched expansion, the strength (especially flexural strength) will decrease. Taking Al2O3 as the standard, the Al2O3 in the product should not be greater than 15%~20%, and 10%~18% is preferred. The main impurity in magnesium aluminate spinel bricks is SiO2, which should not be greater than 1.5%.
Over the past thirty years, people have been pursuing technologies to replace magnesium chrome bricks to eliminate hexavalent chromium pollution, and first placed their hopes on periclase spinel bricks. When spinel bricks entered China with the introduction of six new dry kilns at a price of more than $1,000 per ton, China saw a fever for spinel bricks. The initial reports were optimistic, but gradually different news came from the cement plants: “It can’t hold the kiln skin.” It turns out that the eutectic temperature of spinel bricks and cement is close to (slightly lower) the firing temperature of cement, which is fatal. Therefore, spinel bricks retreated 15~20m in the lining of Chinese cement kilns and reached the upper transition zone. They occupied the position of high-alumina bricks or ordinary magnesia-chrome bricks.
Regardless of M-A series or M-K series products, the academic community agrees that Fe2O3 affects the product’s resistance to atmosphere changes. One of the explanations for the superiority of spinel bricks over magnesia-chrome bricks in the upper transition zone is that the Fe2O3 content is lower than that of M-K series products. However, Yoshiki Tsuchiya of Japan added 4% Fe2 O3 to spinel bricks to improve the brittleness of the bricks. The expansion rate is only 1.13% at 1000℃, the flexural strength is 12MPa, and the wear is 30mm in 8 months in the area of 3840m of φ5.0SP kiln. The wear of commonly used spinel bricks is 80~120mm, and it is said that this high iron brick can hang on the kiln skin when used in the firing zone.
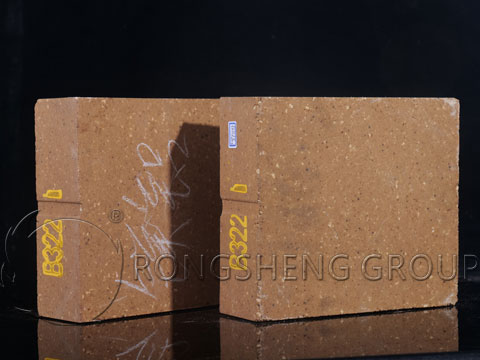
Performance Advantages of Spinel Bricks
Spinel bricks are better than ordinary magnesia-chrome bricks in thermal shock resistance, R+ alkali corrosion resistance, acidic gas corrosion resistance, and atmosphere change resistance. However, for refractory bricks used in transition belts and unloading belts on cement kilns, should also have low thermal conductivity, good wear resistance, and high shear fracture resistance. It determines the availability of spinel bricks. China has been using spinel bricks for about 20 years. The most basic problem exposed is the high cylinder temperature. The cylinder temperature of a 200~220mm thick kiln lining will rise to 350℃ or even close to 400℃ within 100 days of operation. The wear resistance is poor, and it is rare to be able to operate stably for more than 8 months on a 2500t kiln.
The ingredients of periclase spinel bricks in my country use sintered high-purity magnesia sand, medium-grade magnesia sand, and synthetic spinel sand (SiO2 0.6%~2.0%). The thermal shock resistance index is generally more than 10 times, and the best ones are more than 20 times. However, the high-temperature flexural strength is low (1400℃, 0.5h), which is roughly 23MPa, and most products are less than 3MPa. This is a technology that spinel bricks need to improve. Spinel bricks for cement kilns. Magnesium-aluminum spinel bricks for cement kilns.
The advantages of spinel bricks are good thermal shock resistance. During use, they react with clinker to form a very thin calcium aluminate protective layer on the surface of spinel bricks. It makes the liquid phase difficult to penetrate, and the anti-stripping performance is better than that of directly bonded magnesia-chrome bricks. When used in the cooling zone and transition zone of the cement kiln, the service life is doubled compared to that of directly bonded magnesia-chrome bricks. However, it is slightly inferior to directly bonded magnesia-chrome bricks in terms of corrosion resistance. At the same time, spinel bricks are easy to hydrate, have a large thermal conductivity, and the kiln shell temperature is higher than when using directly bonded magnesia-chrome bricks.
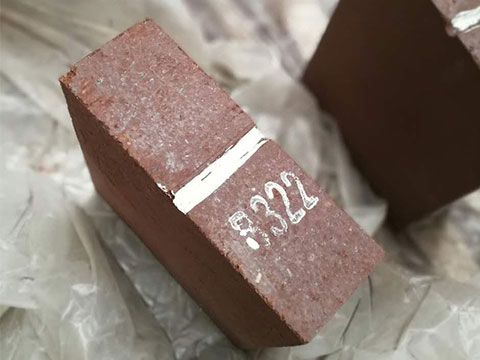
Application of Rongsheng Magnesium Aluminum Spinel Brick in the Transition Zone of Cement Rotary Kiln
Magnesium aluminum spinel brick is a product made of high-purity magnesia sand and pre-synthesized magnesium aluminum spinel as the main raw materials, after reasonable grading, high-pressure molding and high-temperature firing. It is characterized by high strength, corrosion resistance, low linear expansion coefficient, and good thermal shock resistance. It is an ideal refractory material for the transition zone of cement rotary kiln.
Bauxite-based sintered magnesium aluminum spinel uses high-quality alumina with an Al2O3 content of more than 76% and high-quality light-burned magnesium powder with an MgO content of more than 95%. After a multi-stage homogenization process, it is sintered at a high temperature of more than 1800°C in an ultra-high temperature tunnel kiln. It has a large volume density, a high mineral phase content, good grain development, uniform structure, and stable quality. Magnesium aluminum spinel has good erosion resistance, strong corrosion and spalling ability, good slag resistance, abrasion resistance, good thermal shock stability, and high temperature resistance. It is a magnesium aluminum spinel brick for the high temperature zone of the rotary kiln for producing cement. It is also an ideal raw material for refractory products such as ladle lining bricks and ladle castables. Magnesium-aluminum spinel is widely used in refractory materials, steel smelting, cement rotary kilns and glass industrial kilns.
It has good erosion resistance, abrasion resistance and thermal shock stability. Its main uses: First, it replaces magnesia-chrome sand to make magnesia-aluminum spinel bricks for cement rotary kilns, which not only avoids chromium pollution, but also has good spalling resistance. Second, it is used to make ladle castables, which greatly improves the erosion resistance of steel plate linings. It is widely used in refractory materials for steelmaking.
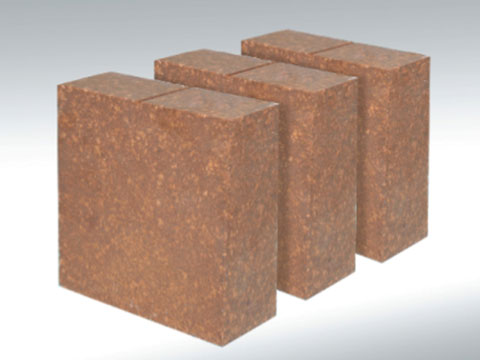
Product Characteristics of Rongsheng Magnesium Aluminum Spinel Bricks
- Excellent kiln skin performance.
- Low thermal conductivity (1000℃, 2.27w/m·k), small thermal expansion coefficient.
- Excellent structural flexibility. The alkali salts of K2SO4, Na2SO4, NaCl, and KCl decomposed from cement materials have strong anti-corrosion and anti-penetration capabilities.
- High load softening temperature and excellent thermal shock resistance. Suitable for key parts of SP and NSP kilns with high kiln temperature, fast rotation speed, strong alkali corrosion ability, and heavy mechanical load. It can effectively extend the life of the furnace lining and maintain a low kiln shell temperature.
Rongsheng Magnesium Aluminum Spinel Brick for Sale from Manufacturer
Rongsheng Refractory Manufacturer, Magnesium Aluminum Spinel Brick is a refractory material with a high melting point, small thermal expansion coefficient, low thermal conductivity, good thermal shock stability and strong corrosion resistance. Magnesium aluminum spinel brick belongs to isometric crystal system minerals, and high-purity magnesium aluminum spinel brick is colorless. Magnesium aluminum spinel crystals formed under natural conditions have good chemical stability, so they are commonly found in drifting sand deposits. Magnesium aluminum spinel crystals with pure composition do not hydrate or react with acid. Magnesium aluminum spinel bricks are made of light-burned magnesium powder, industrial alumina, or high-quality inkstone clay, and are made after cooperative melting, cooling and crushing. The advantages of magnesium aluminum spinel bricks are good crystal development, large grain size, dense structure, and strong corrosion resistance. To purchase high-quality magnesium aluminum spinel bricks for cement rotary kilns, please contact Rongsheng for free samples and quotations.