What Kind of Light Acid-Resistant Castable is Used for Chimney?
The traditional way of lining the chimney is to use acid-resistant cement to build acid-resistant bricks. However, in the masonry mode of acid-resistant brick masonry, the horizontal and vertical joints of the brick are full, which will make the airtightness of the masonry poor. In addition, the dampness of the thermal insulation castable of the thermal insulation layer will cause the thermal insulation performance to decrease. The damage of the heat-insulating castable and the imperfect combination of bricks and bricks will cause corrosive smoke to penetrate the masonry and the insulation layer and corrode the outer cylinder wall. Therefore, the use of lightweight acid-resistant castables for integral casting has also accounted for a certain proportion.
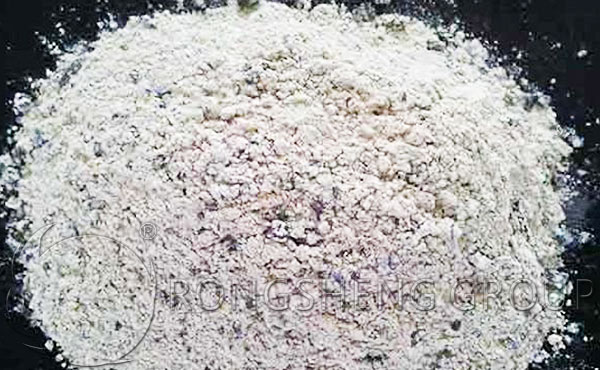
Masonry of the Inner Wall Lining of the Chimney
It is very inconvenient to construct the chimney with the method of heat insulation castable and lined bricks. Practical problems such as the setting of heat-insulating castables, the treatment of the gaps between the bricks, and the moisture-proof measures, have seriously affected the service life of the chimney.
If the thermal insulation castable and the lining of the anticorrosive brick masonry are combined into one. Lightweight or ultra-lightweight acid-resistant castables with strong corrosion resistance, good heat insulation, and high strength are used to make light acid-resistant castable linings by casting. Thermal insulation and corrosion resistance are combined into one, and the overall airtightness has been greatly improved.
Due to the sulfur dioxide in the flue gas in the chimney, there is water in the flue and chimney to form dilute sulfuric acid, and the acid will corrode the acid-resistant castable. Aluminate cement cannot be used as a binder for light acid-resistant castables. Acidic cement will crack and break the lining castables. Therefore, the acid-resistant castable for the chimney lining needs water glass as the binder and aluminate as the cementing agent, which is severely damaged under the action of sulfuric acid.
Acid-resistant Castable for Chimney Inner Wall Lining
Lightweight acid-resistant castables are mainly composed of raw materials and curing agents. The curing agent adopts ammonium phosphate or ammonium chloride or sodium fluorosilicate, which shall not be crushed and used. After stirring, the light acid-resistant castable with a specific gravity of 0.8-1.0. The initial curing time of the light acid-resistant castable is 40 minutes. It is poured into the template and formed in 2 hours. After 24 hours, it is demoulded and then dried naturally. Because the lightweight acid-resistant castable has good sulfuric acid corrosion resistance, it can fully meet the anti-corrosion requirements of the chimney for lining materials.
The light acid-resistant castable is cast as a whole, which can make the lining integrated and airtight, and has a light volume, and also reduces the weight pressure of the chimney.

Advantages of Acid-Resistant Castable
Acid-resistant castables have good strength and stability when immersed in acid. Generally, the compressive strength increases as the immersion time increases. The advantages of acid-resistant castables are as follows.
- Good heat resistance. Lining in the titanium dioxide rotary kiln, the service temperature is as high as 950℃-1000℃.
- The acid-resistant castable has stable performance in various concentrations of organic acid and inorganic acid, especially in dilute acid, industrial water, and neutral aqueous solution without crystal salt. Has high impermeability.
- Acid-resistant castable adopts a non-toxic curing agent, which is non-toxic to operators and construction personnel. Approved by the medical and health department, it can be used in anti-corrosion engineering of food, medicine, and other equipment.
- Curing at room temperature, simple construction, convenient use, easy to transport, and moisture-proof storage. Compared with organic acid-resistant materials, acid-resistant castables are inexpensive. In addition to having the same properties as organic acid and corrosion resistance, it also has the unique performance of resistance to strong oxidizing media.
Acid-resistant castables are suitable for the lining of petrochemical and corrosive equipment. It can fully resist the erosion of acid gases and solutions and is widely used in equipment such as steel chimney lining, flue sulfuric acid tank lining, blast furnace hot blast stove top protective layer, and other equipment.
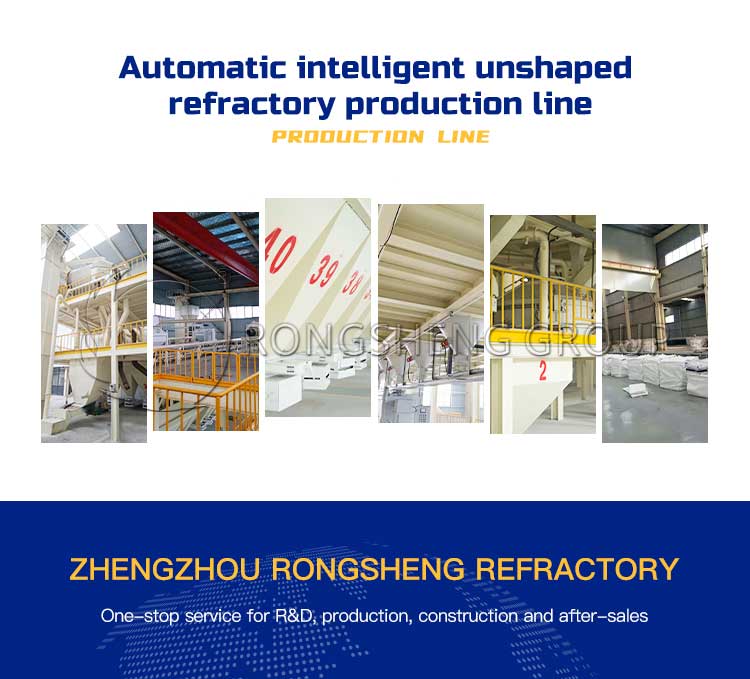
Rongsheng Acid-resistant Castable Manufacturer
Purchase high-quality acid-resistant castables for chimneys from Rongsheng refractory manufacturers. Rongsheng’s advanced environment-friendly and fully automatic unshaped refractory production line have an annual output of tons. If you need to buy various unshaped refractory lining materials, please contact us. We will provide you with high-quality refractory castable products suitable for your production needs according to your specific needs.