Production and Application of Sillimanite Bricks for Blast Furnace
Due to the characteristics of its raw materials, sillimanite bricks have a low thermal expansion rate, resistance to metallurgical slag and various glass liquids, and high temperature abrasion resistance. Therefore, the physical and chemical properties of sillimanite bricks are better than those of high-alumina bricks, with a fire resistance of 1770 ~ 1830 ℃ and a load softening starting point of 1500 ~ 1650 ℃. It is mainly used for forming the liquid hole of the glass pool kiln, the lining of the blast furnace, the throat and the ceramic industrial kiln furniture.
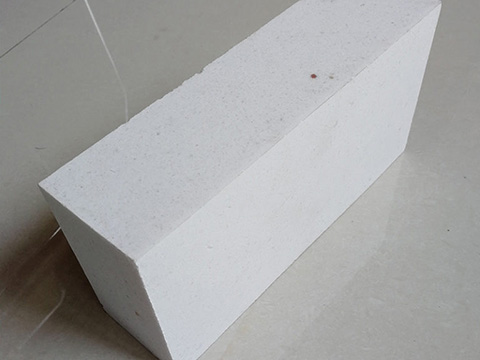
Sillimanite Bricks Manufacturer #1
The blast furnace sillimanite bricks produced by the plant are based on sillimanite and mullite, alumina clinker and cokestone clinker as aggregates. It is made by adding an appropriate amount of bound clay and mixing with the granules at an appropriate ratio, after mixing, high pressure molding and proper firing temperature.
Physical and Chemical Index of Sillimanite Bricks for Blast Furnace
Items | Sillimanite Bricks (#1) |
Apparent Porosity (%) | 15.3 |
Bulk Density (g/cm3) | 2.58 |
Cold Crushing Strength (MPa) | 120.9 |
Refractoriness (℃) | >1810 |
Refractoriness Linear Change (%) (1500℃, 2h) | +0.17 |
KD | 1590 |
T2 | 1660 |
Thermal Shock Resistance (1000,WaterQuenching, Cycle) | >15 |
The Main Chemical Composition of Sillimanite Bricks Raw Materials
Items | Al2O3 | Fe2O3 | TiO2 | K2O+Na2O |
Sillimanite | 57.33 | 1.71 | 0.91 | 0.49 |
Grade II bauxite clinker | 67.68 | 1.30 | 1.65 | 0.30 |
Grade I bauxite fines | 82.50 | 2.40 | – | – |
Mullite | 76.17 | 0.40 | 0.27 | 0.50 |
Flint Clay Clinker | 44.61 | 1.20 | – | – |
Production Process of Sillimanite Bricks for Blast Furnace
The firing temperature of sillimanite brick is between 1350 ~ 1400 ℃. This is a major feature of process parameters. Firing is performed in a tunnel kiln. And in summary, the addition of sillimanite to high-alumina materials (such as rocky soil, mullite, etc.) can produce high-quality refractories.
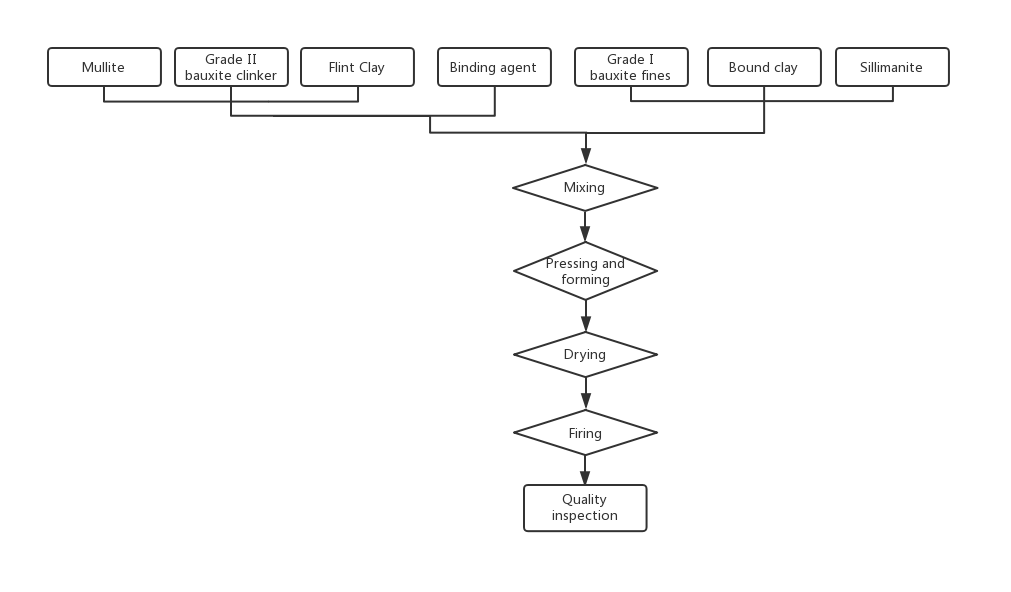
Sillimanite Bricks Manufacturer #2
Sillimanite bricks for blast furnaces. The parts used are furnace bottom protection brick, furnace throat lining and tuyere combination brick.
The brick is made of sillimanite, andalusite and sintered mullite as the main raw materials, and some ultrafine powders and binders are added. The bricks are fired in a tunnel kiln by high pressure molding or vibration pressure molding. The firing temperature is 1390 ~ 1400 ℃, and the heat preservation time is 10 ~ 16h.
The proportion of sillimanite bricks: sillimanite 30% to 40%, andalusite + mullite 35% to 55%, super alumina 10% to 15%, raw clay 5% to 10%.
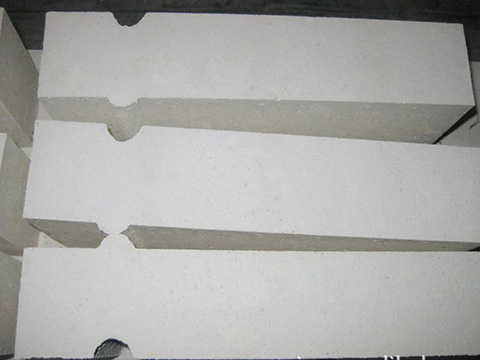
Physical and Chemical Index of Sillimanite Bricks for Blast Furnace
Items | Refractoriness(℃) | Apparent Porosity (%) | Bulk Density (g/cm3) | Cold Crushing Strength (MPa) | T2 | Thermal Shock Resistance (1000,WaterQuenching, Cycle) | Al2O3 | Fe2O3 | Refractoriness Linear Change (%) (1500℃, 2h) | Thermal Expansion (1000℃,%) |
Sillimanite Bricks (#1) | >1790 | 13 | 2.58 | 99.6 | 1610 | >30 | 61.28 | 0.86 | 0 | – |
The sillimanite bricks produced by the plant use sillimanite and andalusite composite materials. Particle size of sillimanite concentrate: 0.250 ~ 0.149mm, about 10% ~ 20%, 0.149 ~ 0.104mm, about 27% ~ 60%, 0.104 ~ 0.074mm, about 12% ~ 28%, and less than 0.074mm, about 30% ~ 48%. This particle size is used as an intermediate particle when making bricks.
The decomposition temperature of andalusite is different from that of sillimanite. At the calcination temperature of about 1400 ° C, the sillimanite crystals in the product have not been transformed, and the transformation of andalusite crystals is not complete. Therefore, during use, these crystals continue to undergo the micro-expansion accompanied by mullite , Which is enough to offset the shrinkage caused by the increase of the liquid phase amount of the product at high temperature, and improve the load softening temperature of the product. At the same time, high pressure molding plays a role in reducing porosity and increasing strength.
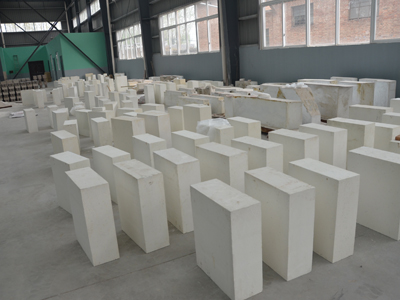
Conclusion
In summary: Over the years, users have reported good use and can better meet the needs of the light industry, building materials, and metallurgical industries. Due to the good physical and chemical properties, low cost, and significant economic and social benefits of Sillimanite Bricks products, its development prospects are very broad. The Sillimanite Bricks products need to further improve its physical and chemical properties.