Compactness of Magnesia-Aluminum Spinel Rich in Magnesium Oxide
Application of magnesia-alumina spinel bricks in cement kilns. At present, the chromium-free measures taken by the new dry process cement kiln are mainly to replace magnesia-chrome bricks with magnesia-dolomite bricks, magnesia-alumina spinel bricks, and magnesia-iron-alumina spinel bricks (referred to as magnesia-iron bricks). Its kiln lining performance is very outstanding, and it is the best material to replace magnesia-chrome bricks in domestic cement kilns.
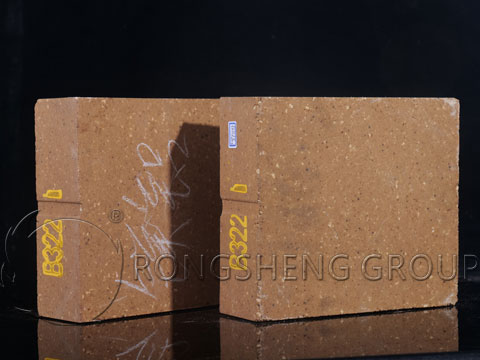
The magnesia-alumina spinel bricks produced by introducing ferroalumina spinel into magnesia refractory materials provide a new lining concept for cement rotary kilns. Its good structural flexibility and excellent kiln lining performance provide it with high adaptability. In recent years, magnesia-alumina spinel bricks have been fully used in the high-temperature zone of cement rotary kilns. Rongsheng refractory manufacturer can provide high-quality magnesia refractory brick products for cement kilns, including magnesia-dolomite bricks, magnesia-alumina spinel bricks, and magnesia-alumina spinel bricks. Contact Rongsheng for a free quote.
Material Properties of Magnesia-Alumina Spinel
Magnesia-alumina spinel is one of the most important refractory materials in the steel and cement industries. It has gradually replaced chromium spinel and is also a popular refractory material in the above fields. However, magnesium-chromium alloys and Al2O3-chromium alloys are gradually decreasing due to the environmental hazards of hexavalent chromium. Magnesium-alumina spinel has excellent refractory properties such as high refractoriness, moderate thermal expansion, thermal shock stability and resistance to slag erosion.
The densification of spinel by primary firing requires very high temperatures (>1700℃) because the oxide composition is accompanied by a 7% volume expansion during the spinel formation process. On the other hand, the expansion during the spinel formation process is beneficial for Al2O3-MgO-C (AMC) bricks. Because the expansion during the in-situ spinel formation process minimizes the gaps between bricks and prevents metal infiltration.
The formation and sintering of spinel have been studied by different researchers by changing the raw materials and processing steps. Mansour et al. pointed out that the most spinel is formed when the calcination temperature of raw materials MgCO3 and Al(OH)3 is 900℃ and 1100℃ respectively. Gray believes that hydroxide contributes to the formation of spinel and the densification of magnesium-aluminum spinel. Kostic et al. found that fine grinding of raw materials will increase its specific surface area and increase its structural defects, which will lead to the formation of low-temperature spinel.
Magnesia-Rich Magnesia-Alumina Spinel
Magnesia-rich magnesia-alumina spinel is mainly used in cement kilns because of its compatibility with the products of cement formation process. Compactness of MgO-rich magnesia-aluminum spinel. Alper in the study of MgO-Al2O3 binary system showed that the solubility of MgO in the spinel phase was 39%. Bailey et al. found that the presence of excess MgO in the spinel phase would restrict the growth of spinel grains and promote sintering. Cooper et al. found that 40% MgO in magnesia spinel bricks would improve its thermal and corrosion properties. India has a large reserve of magnesia ore, which contains impurities such as CaO, SiO2 and Fe2O3 that limit its application at high temperatures. In the present study, natural magnesia ore has harmful impurities SiO2 and CaO. As a magnesia-rich magnesia-alumina spinel aggregate, it was developed and compared with the aggregate prepared by synthetic calcined magnesia.
Dense Magnesium Aluminate Spinel
Through various experiments, researchers have a unique understanding of dense magnesium aluminate spinel bricks.
1) The density of sintered spinel generated by Salem magnesite (SS) increases sharply between 1400℃ and 1500℃, followed by a slight decrease at higher temperatures due to liquid phase sintering. The spinel generated by caustic magnesia (NS) densifies slowly below 1500℃, followed by an improvement in density at 1600℃. The NS sample is densified by solid phase sintering.
2) X-ray diffraction analysis of the SS sample sintered at 1600℃ shows that spinel and periclase are the main phases, and forsterite is the secondary phase. This is because SiO2 exists in natural magnesite, while the NS sample only contains periclase and spinel phases.
3) As the temperature increases from 1500℃ to 1600℃, the flexural strength of the NS sample increases due to its more compactness. However, compared with the SS sample sintered at 1500℃, the flexural strength of the SS sample sintered at 1600℃ is lower, which is due to the presence of the low melting point phase and the uneven particle size distribution.