8 Characteristics of Honeycomb Ceramic Catalyst Carrier
The main material of honeycomb ceramic carrier is cordierite. The honeycomb ceramic material used for automobile exhaust treatment is often porous cordierite, which mainly provides an inert physical structure for carrying the catalyst coating. The thermal expansion coefficient of cordierite is 2.9X10-6/℃. The melting point is about 1460℃, and it has good thermal stability. Cordierite has two homogeneous multiphase variants, namely low-temperature cordierite and high-temperature cordierite. High-temperature cordierite is also known as Indialite, which belongs to the hexagonal system; low-temperature cordierite is what people usually call cordierite, which belongs to the orthorhombic system. Rongsheng cordierite honeycomb ceramic manufacturer provides high-quality cordierite honeycomb ceramic products. Contact Rongsheng for detailed information.
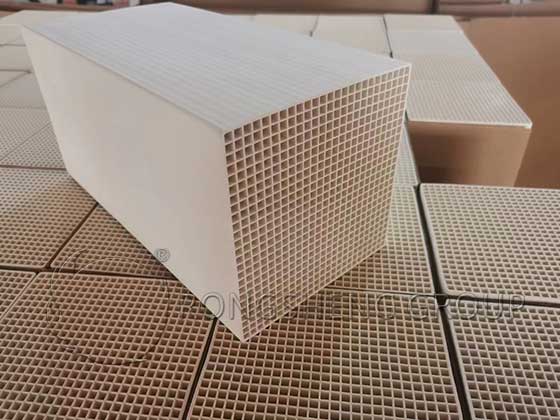
Honeycomb Ceramic Catalyst Carrier
In order to have a larger catalytic surface in a smaller volume, the surface of the catalyst carrier is made into a honeycomb shape. The biggest advantage is that it has a large specific surface, a low thermal expansion coefficient, excellent thermal shock resistance, strong acid and alkali resistance and corrosion resistance, and has high mechanical strength.
As a carrier, honeycomb ceramic is a key component of the three-way catalytic converter. One of its important materials is cordierite, which is resistant to high temperatures, has a high continuous operating temperature of up to 1200°C, high strength and low linear expansion coefficient. The carrier adopts an effective surface and a suitable pore structure. The ceramic carrier has an opening rate of 400-600 mesh/inch2 and a minimum wall thickness of about 0.16mm. It can enhance the mechanical strength of the catalyst, and also improve its resistance to wear, impact, gravity, pressure, high temperature and phase change. Improve the conductivity of the catalyst and reduce the content of active components. Especially when using precious metal catalysts such as platinum, palladium and rhodium, the active components can be highly dispersed and the dosage can be reduced.
In short, the quality of the carrier is extremely important for the catalyst. The mesh number of the honeycomb ceramic carrier can be 200 mesh, 300 mesh, 400 mesh or 600 mesh. The cross-sectional shapes include circular, racetrack, elliptical and some special shapes according to customer requirements, in order to meet the needs of different application conditions.
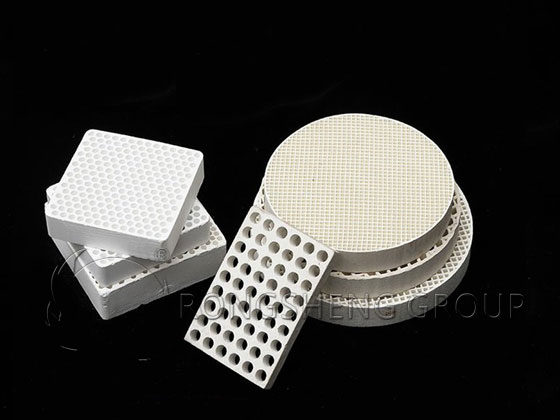
Characteristics of Honeycomb Ceramic Catalyst Carrier
Honeycomb ceramic catalyst carrier has eight significant advantages, as follows:
- Thin pore wall, large specific surface area, low resistance, low bulk density, high compressive strength.
- Small thermal expansion coefficient.
- Good thermal shock resistance and thermal shock resistance.
- Good matching with various catalyst active components.
- Good cold start performance, low ignition temperature, fast heating, small gas resistance, high conversion efficiency.
- Spiral, double S and three-core core structures can be produced according to user requirements.
- It can be designed into cylindrical, runway and other special-shaped structures according to the requirements of different motor vehicles.
- The product meets the manufacturing and supporting requirements of various scales and models of motor vehicles and meets Euro III and more stringent emission standards.
Application of Cordierite Ceramics
Square mirrors for photolithography
As one of the core units of a photolithography machine, the motion accuracy of the ultra-precision worktable directly affects the resolution of the photolithography machine. As the core component of the worktable, the square mirror guarantees the accuracy of the worktable and the efficiency of photolithography. The thermal load on the square mirror during operation will change continuously due to the influence of the heat flow in the working space, requiring its deformation to change as little as possible with temperature. At the same time, it is also necessary to deal with the distortion correction caused by its operation at higher acceleration and speed. Therefore, in order to meet the requirements of photolithography accuracy, the thermal expansion coefficient of the square mirror material must achieve near-zero expansion at the working temperature, and it must also have good mechanical properties. Cordierite ceramics are ideal materials for square mirrors for photolithography machines due to their low thermal expansion coefficient, excellent mechanical properties and low density. ASML has achieved mature application and promotion of cordierite ceramics in the mobile platform components of photolithography machines.
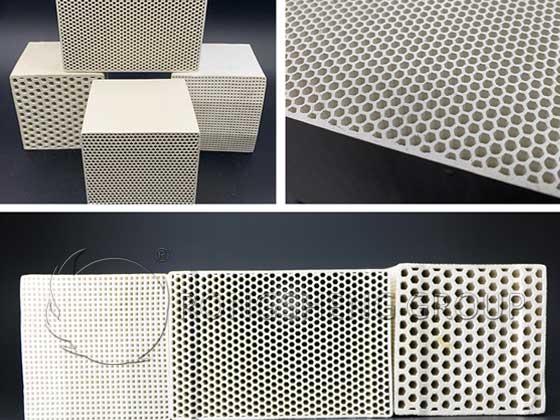
Optical mirrors for optical communication
Cordierite has the characteristics of low thermal expansion, high mechanical strength and high rigidity, long-term dimensional stability, and radiation resistance, and can be used in space optical communication. Sony CSL has adopted Kyocera cordierite ceramic mirrors for small near-Earth orbit security laser communication terminals.
Refractory materials
Cordierite ceramics are often used as ceramic packaging materials and kiln tools during the use of kilns due to their low thermal expansion coefficient. At the same time, cordierite ceramics have the characteristics of low density, low thermal conductivity and good high-temperature stability, and can also be used in heat exchange devices with fast temperature changes, such as heat-resistant pots. There are a large number of gaps between the six-membered rings of cordierite crystals and between the upper and lower adjacent six-membered rings. This loose crystal structure gives it an extremely low thermal expansion coefficient, and can be used as a lost foam refractory coating during the casting process, improving the precision of the casting.
Catalyst carrier
Cordierite has a loose crystal structure and a low thermal expansion coefficient, so it can be made into a porous cordierite catalyst carrier. The service environment of the catalyst carrier material is complex and has high requirements for material performance. In particular, the monolithic catalyst used for automobile exhaust treatment, during the operation of the engine, due to the effect of thermal shock, the temperature of the exhaust gas rises to about 700°C in a few seconds. When the engine stops, the temperature drops rapidly to the ambient temperature. A good automobile exhaust monolithic catalyst needs to repeat this process thousands of times, and the carrier needs to support the catalyst and ensure mechanical strength. Cordierite ceramics also have good thermal shock resistance, thermal shock resistance, chemical stability and certain mechanical strength, and are also widely used in water pollution treatment.
Microwave communication dielectric materials
Cordierite ceramics have a low dielectric constant and a near-zero frequency temperature coefficient. It is an ideal low-dielectric high-frequency microwave dielectric ceramic, which is used in the preparation of electronic packaging dielectric resonant antennas, microwave device substrates, high-end microwave components and other devices.