High-strength Corundum Castable RS Refractories Manufacturer
High-strength Corundum Castable are fire-resistant crafts with Al2O3 content exceeding 90%, with corundum as the main crystal phase, and blended with appropriate thickeners, coagulants, stainless steel plate chemical fibers, and compounded according to strict secret recipes. It has many characteristics such as good high temperature compressive strength, wear resistance, erosion resistance, high heat transfer, thermal shock resistance, corrosion resistance, good air tightness and early strength by the High-strength Corundum Castable RS Refractories Manufacturer. Email us for more details.
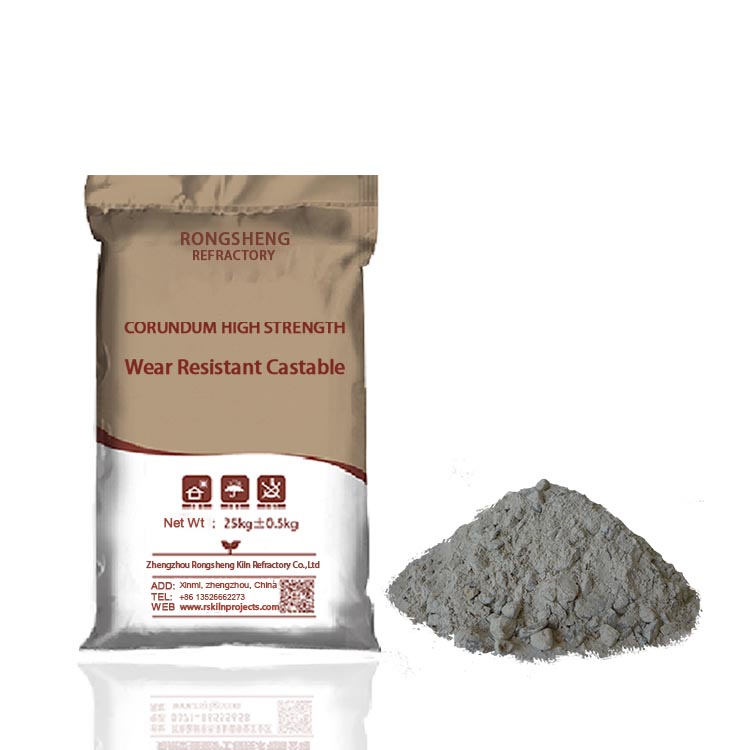
High-strength Corundum Castable Description
Corundum series castable refractory products are a type of unshaped refractory insulation materials that are relatively common in production and application at this stage. Corundum is a high-strength abrasion-resistant and refractory castable raw material. The key is to use corundum as the stone and particulate material plus some fusion agent to prepare the refractory castable. Compared with high aluminum refractory castable and mullite refractory castable, it has higher impact toughness and cavitation resistance. It is mainly used as lining raw materials for various furnaces such as heating furnaces, hot blast furnaces for ironmaking blast furnaces, heat treatment furnaces, and porcelain kiln. The castables are mainly used in metallurgical industry and industrial furnaces, and are also widely used in crude oil, chemical plants, decorative building materials, electrical engineering and mechanical equipment industrial furnaces and thermal insulation equipment. It is mainly used to construct a variety of general buildings such as heat treatment furnace linings.
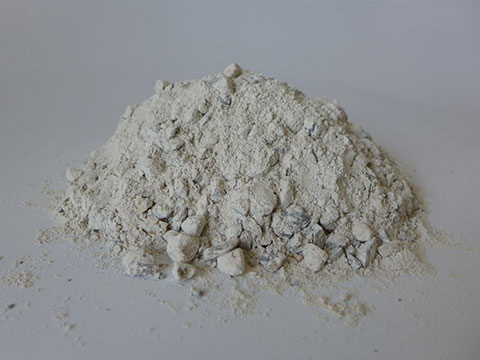
High-strength Corundum Castable Uses
(1) Adding steel fiber and water reducing agent to the castable can produce steel fiber castable with good heat resistance and strong wear resistance. Mostly used for heat treatment furnace hearth, tapping trough and cement rotary kiln mouth.
(2) According to customer requirements, using this series of product castables can be used to produce and process a variety of prefabricated components.
High-strength Corundum Castable Physical and Chemical Indicators
Chemical Composition(%) | AL2O3≥ | 70 | 75 | 80 | 85 |
SiO2≤ | 26 | 21 | 16 | 11 | |
CaO≥ | 2.5 | 1.5 | 1.2 | 1.0 | |
Modules of Rupture(MPa) | 110℃×24h≥ | 8 | 11 | 12 | 13 |
815℃×3h≥ | 9 | 12 | 13 | 14 | |
1100℃×3h≥ | 10 | 13 | 14 | 15 | |
Cold Crushing Strength(MPa) | 110℃×24h≥ | 70 | 80 | 85 | 90 |
815℃×3h≥ | 80 | 85 | 90 | 95 | |
1100℃×3h≥ | 85 | 90 | 95 | 110 | |
Bulk Density (g/cm3) | 2.75 | 2.85 | 2.9 | 2.95 | |
CC ≤ | 7 | 6 | 6 | 5 | |
Thermal Shock Resistance (900℃water quenching),cycle ≥ | 25 | 20 | 25 | 20 | |
Features | Abrasion resistance, erosion resistance, high use temperature, long life and easy construction. |
Instructions for use of High-strength Corundum Castable
1. Before construction of the refractory castables project, be sure to check whether the nails are firmly welded. Use high temperature resistant nails at around 500 ℃. The surface of the nails should be coated with paint or plastic tape to buffer the surging ground stress after heat.
2. The pouring material should be stored in a warehouse with a cover to prevent the return of moisture. The storage period cannot exceed six months.
3. It can be applied in the working temperature range of -5 ℃ ~ 30 ℃.
4. In the application, be sure to use a forced mixer or mortar mixer to mix materials, and do not use manual service to mix materials. The mixing utensils need to be cleaned and tidy in advance. Do not infiltrate other dirt such as lime powder, grit, fly ash cement.
5. Be sure to use clean drinking water for mixing, strictly control the water demand, and perform measurement verification.
6. Add the big bag material first, then the small bag material, and then add the water. The water flow rate refers to the water demand of each model. After mixing with water for 3 minutes, tap water can be removed from the blender by holding the ginseng pellets. Under the condition that the slurry can be shaken, tap water is required to achieve higher compressive strength.
7. During the application, all the raw materials in the bag should be cleaned, and some of the applications cannot be removed. It is forbidden to mix different types of castables.
8. The construction time can be up to 30 minutes. The solidified blocks can not be mixed with water and used, and should be abolished. Large and medium-sized stirring rods are used to vibrate, which exceeds the compaction density. The massage stick must be reserved. In case that the massage stick is abnormal, the reserved stick can be turned on immediately.
9. The lining can be dismantled every day after construction, and it can be maintained in natural gas every day. If it needs to be delivered, it can be baked.