Magnesia Dolomite Bricks Description
Magnesia dolomite brick is a kind of MgO-CaO basic firebrick, which can be divided into lime dolomite brick, dolomite brick, and magnesia dolomite brick. In lime dolomite bricks, CaO and MgO molecular ratio is larger than 1, in dolomite bricks, CaO and MgO ratio is equal to 1, while in magnesia dolomite bricks, the molecular ratio of CaO and MgO is less than 1. Magnesia dolomite adopts dolomite sand, magnesia dolomite sand, and magnesia sand as raw material. After mixing with a water-free binder, high-pressure molding, and high-temperature sintering, magnesia dolomite is finally produced. Magnesia dolomite bricks’ raw material should have high purity(high CaO and MgO content), low porosity, and high density. Free CaO, Fe2O3, SiO2, and Al2O3 are harmful impurities, as they can affect slag resistance and the high-temperature performance of magnesia dolomite bricks.
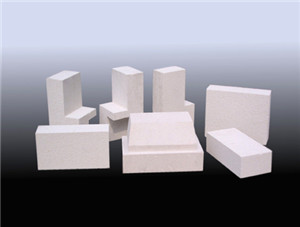
Magnesia Dolomite Bricks Property
- Low porosity, high density.
- Basic slag corrosion resistance and cement clinker corrosion resistance.
- High refractoriness, lowest eutectic point temperature is 2370℃.
- High refractoriness under load temperatures, higher than 1700℃.
- MgO-CaO material has a desulfurization function and is good for cleaning steel production.
- Won’t contaminate steel liquid, easy to remove impurities in steel liquid.
Magnesia Dolomite Bricks Application
Different models of magnesia dolomite bricks should be adopted according to different applications. When CaO content in MgO-CaO series refractory is between 20%~40%, there will produce a relatively low quantity of liquid phase under the corrosion of steel refinery furnace slag( low alkalinity slag), meanwhile, the average dissolving speed is slow. The higher MgO/CaO ratio is, the better corrosion resistance and creep resistance is, but spalling resistance will be lower. Dolomite bricks have better cement kiln coating adhesion properties than magnesia dolomite bricks, but worse cement clinker corrosion resistance.
Magnesia dolomite bricks are widely used in out-furnace refinery furnaces such as AOD, VOD, LF furnaces, and so on. For example, when applied in an AOD furnace, high-density zirconia-bonded magnesia dolomite bricks are used at the tuyere and adjacent parts. The rest part of the furnace wall can adopt ordinary sintered magnesia dolomite bricks. In large-scale cement kilns, magnesia dolomite bricks are a good replacement for magnesia chrome bricks and have a wider and wider application.
Application of magnesia dolomite refractory bricks for VOD/VAD furnaces
The use of magnesia dolomite bricks is becoming more and more extensive, especially in AOD furnaces. The world’s stainless steel production is on the rise, and more than 75% of stainless steel production uses the AOD method. At present, the refractory materials used in AOD furnaces are mainly dolomite bricks, magnesia dolomite bricks, and magnesia chrome bricks. Magnesia-chrome bricks are used in the United States, fired dolomite refractory bricks are used in Germany, unfired dolomite bricks are mainly used in Italy, magnesia-chrome bricks are used in Japan, and pure dolomite bricks are used in Europe. The use effect of magnesia dolomite bricks is better than that of magnesia chrome bricks. From the perspective of development trends, magnesia calcium bricks will replace magnesia chrome bricks. When smelting stainless steel, it is better to use unburned magnesia calcium carbon bricks.
At high temperatures in the VOD furnace, highly corrosive slag is produced, and there is a strong eddy current. In order to reduce the recarburization of the refractory lining, a carbon-free thermodynamically stable wear-resistant material should be used. Here, fired dolomite or dolomite magnesia refractory bricks should be preferred. In terms of corrosion resistance and economic benefits, magnesia dolomite bricks (MgO78.7%, CaO19.5%) are better than magnesia chrome bricks.
VAD refining ladle is mainly used for refining carbon steel and alloy steel with high purity requirements. Magnesia-chrome bricks are generally used for the slag line, and now they are developed into dolomite, magnesium-dolomite, and high-purity dolomite carbon bricks, with a service life of 30 to 40 times, while magnesia-chrome bricks are less than 15 times. The erosion rate of the slag line of a 60t VAD furnace in a steel plant is only 33.1%~42.7% of that of high-strength magnesia-carbon bricks.
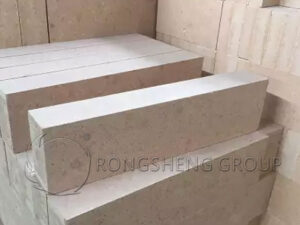
Burnt oil-impregnated magnesia dolomite brick for AOD furnace
The main raw material of magnesia dolomite bricks is magnesia dolomite sand, according to reasonable gradation, high-pressure forming bricks. It is fired at 1600°C and then vacuum-impregnated. The fired oil-soaked brick has high purity, the total impurity content of SiO2+Al2O3+Fe2O3 is not more than 3%, and the density is high. The structure of the brick is characterized by the formation of direct bonds between the main crystals in the clinker particles. The particle gap is filled with pitch carbon and the carbon content in the brick increases by about 2.5%. A uniform asphalt film is formed on the surface of the product to prevent hydration, prolong the shelf life of the product and improve the quality of the brick. The use performance is improved, and the physical and chemical properties of fired magnesia dolomite refractory bricks are compared.
An 18t AOD refining furnace for smelting stainless steel has achieved good results by using fired oil-impregnated magnesia dolomite bricks. The average furnace age is 40 furnaces when the lightweight insulation bricks are used in the extremely high erosion area of the vulnerable parts – the tuyere bricks and the bricks around the tuyere area are not matched. The highest can reach 45 furnaces, which is about 25%~30% longer than the life of magnesia-chrome bricks. The corrosion resistance is better than that of pre-reaction magnesia-chrome bricks, and the remaining bricks after use are 150~250mm. The products have good performance and application potential.
Cement rotary kiln magnesium dolomite bricks
Sampling and analysis of residual magnesium dolomite bricks used in the harsh firing zone of a cement rotary kiln in a factory. Magnesia dolomite brick itself has good cement clinker affinity, good resistance to sulfur and alkali erosion, and high-temperature performance. The magnesia dolomite refractory brick improved by introducing zirconia can be suitable for the kiln condition requirements of the cement rotary kiln firing zone. Especially when the prices of mainstream materials for magnesia-iron spinel bricks and magnesia-alumina spinel bricks remain high. It is a technically feasible and very economical choice to choose magnesia dolomite bricks for use in the firing zone of cement rotary kilns.
Magnesia Dolomite Bricks Physiochemical Index
Item | MDZ15 | MDZ20 | MDZ25 | MDZ30 | MDZ40 | MDZ50 |
MgO % | 80.3 | 76.3 | 70.3 | 66.3 | 56.3 | 43.3 |
CaO % | 17 | 21 | 27 | 31 | 41.0 | 54 |
Al2O3 % | 0.5 | 0.5 | 0.5 | 0.5 | 0.5 | 0.5 |
Fe2O3 % | 0.7 | 0.7 | 0.7 | 0.7 | 0.7 | 0.7 |
SiO2 % | 1.3 | 1.3 | 1.3 | 1.3 | 1.2 | 1.3 |
Bulk density g/cm3 | 3.03 | 3.03 | 3.03 | 3.03 | 3.0 | 2.93 |
Apparent porosity % | 13 | 12 | 12 | 13 | 13 | 12 |
Compression strength Mpa | 80 | 90 | 80 | 80 | 80 | 70 |
RUL ℃ | 1700 | 1700 | 1700 | 1700 | 1700 | 1700 |
High-temperature rupture strength Mpa | 2.5~4.5 | 2.5~4.5 | 2.5~4.5 | 2.5~4.5 | 2.5~4.5 | 2.5~4.5 |
Thermal conductivity w.(m.k)-1 | 3~4 | 3~4 | 3~4 | 3~4 | 3~4 | 3~4 |
Dolomite Bricks Manufacturers
Alkaline refractories produced with dolomite as the main raw material are called dolomite refractory materials. According to its chemical mineral composition, dolomite refractory materials can be divided into two categories.
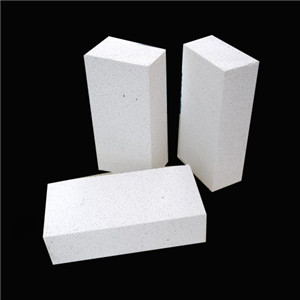
(1) Dolomite refractory materials containing free lime. Because its composition contains active CaO that is difficult to sinter, it is easy to absorb moisture and pulverize, so it is also called unstable or non-water-resistant dolomite refractory material.
(2) Dolomite refractory without free CaO. Its mineral composition is MgO, C3S, C2S, CAF, C2F (or CA). The CaO in the composition is all in a bonded state and will not be powdered due to hydration, so it is also called a stable or water-resistant dolomite refractory material. Stabilized dolomite refractory bricks fall into this category. This kind of product can be used to build an open hearth furnace wall and furnace bottom, rotary kiln and shaft kiln firing zone, etc., but it is rarely produced at present.
Dolomite refractory materials are mainly used as linings of basic oxygen converters. From the perspective of chemical composition, it has gone through the stages of impurities from high to low, and from non-fired to lightly fired to high-temperature fired in terms of technology. The current general trend is to develop low impurity levels. Synthetic dolomite bricks with high MgO content. With the rapid development of oxygen top-blown converter steelmaking, dolomite refractory materials in my country have also been developed rapidly. New varieties and new techniques are constantly appearing, such as large bricks formed by vibration, light-fired vacuum oil-impregnated bricks, synthetic magnesia dolomite large bricks, and fired oil-impregnated dolomite bricks, etc. Both have been successfully used in the converter, greatly improving the life of the furnace.