The ceramic cup technique is invented by France SAVOIE company. The ceramic cup technique synthesized furnace bottom and furnace hearth by different kinds of composite refractory materials and constructed into a closed ring type furnace lining, i.e. ceramic cup. The inner lining is built by low thermal conductivity, high rupture under load, and corrosion-resistant ceramic refractory materials, while the outer side adjacent to the cooling wall is built by high thermal conductivity micro pore carbon bricks. So iron slag produced in the blast furnace will directly contact with ceramic lining, which can not only reduce heat loss but also protect carbon brick from corrosion. Thus, the furnace lining’s service life can be prolonged significantly.
Usually used ceramic cup blocks are composite brown corundum brick, corundum mullite brick, micropore corundum brick, and composite carbon brick.
1. Composite brown corundum brick
Composite brown corundum brick’s raw materials are brown corundum, silicon carbide, additives, and binder. The final products are made by mixing, high-pressure molding, sintering in reducing atmosphere, and fine grinding. Composite brown corundum brick is mainly used for blast furnace ceramic cup, furnace bottom, tuyere, cinder notch, and so on.
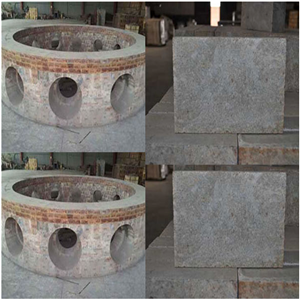
Composite brown corundum brick characteristics
- Strong iron liquid corrosion resistance, alkaline molten slag corrosion resistance.
- Iron liquid scouring resistant, strong self-healing ability.
- Long service life
Composite brown corundum brick physiochemical index
Item | Index |
Al2O3 % ≥ | 78 |
SiC % | 8-14 |
Fe2O3 % ≤ | 1.0 |
Bulk Density g/cm3 ≥ | 2.9 |
Apparent Porosity % ≤ | 15 |
Cold Compression Strength Mpa ≥ | 100 |
0.2Mpa Rupture Under Load ℃ ≥ | 1660 |
Permanent Liner Change % | ±0.2 |
Thermal Expansion % | 0.5 |
Slag corrosion resistance % ≤ | 10 |
2. Mullite Corundum Brick
Mullite corundum brick adopts tabular corundum or fused (sintered) corundum, fused or sintered mullite as main raw materials, added with ultra micro mullite powder and corundum powder, binder, and additives, then carry on mixing, static compression molding, drying, and finally sintered in a high-temperature kiln.
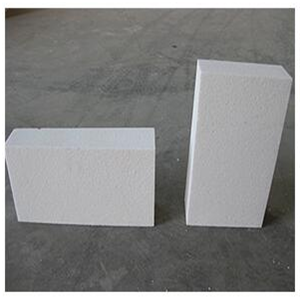
Mullite Corundum brick characteristics
- High refractoriness, good scouring resistance.
- Stable chemical property.
- Strong iron liquid and molten slag corrosion resistance.
Mullite corundum brick physiochemical index
Item | Index |
Al2O3 % ≥ | 80 |
Fe2O3 % ≤ | 1.5 |
CCS MPa ≥ | 80 |
BD g/cm3 ≥ | 2.85 |
AP % ≤ | 19 |
0.2MPa RUL ℃ ≥ | 1550 |
PLC 1500℃*2h % | ±0.2 |
Refractoriness ℃ ≥ | 1790 |
3. Micropore Corundum Brick
Micropore corundum brick uses fused tight corundum as the main material, mullite, silicon powder, silicon carbide fine powder as fines, and proportionally added with binder and additives. By adequate even mixing, molding, drying, and sintering in a high-temperature kiln, micropore corundum brick is produced. During production, special micro pore manufacturing craft is adopted which promises the high density of the corundum brick. Micropore corundum brick is suitable for places of blast furnace such as a ceramic cup, tuyere, tapping hole, and cinder notch.
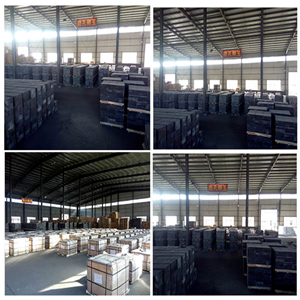
Micropore corundum brick characteristics
- Strong alkaline slag corrosion resistance.
- Strong iron liquid permeation resistance.
- Good iron liquid corrosion resistance.
- Good high-temperature compression Strength.
Micropore Corundum brick physiochemical index
Item | Index | |
RSMC-1 | RSMC-2 | |
Al2O3 % ≥ | 80 | 85 |
Fe2O3 % ≤ | 1.0 | 0.8 |
CCS Mpa ≥ | 100 | 120 |
Bulk Density g/cm3 ≥ | 3.10 | 3.20 |
AP % ≤ | 16 | 14 |
Transparency mDa ≤ | 1.0 | 0.5 |
Iron Liquid Corrosion index % ≤ | 1.5 | 1.0 |
Slag corrosion resistance % ≤ | 8 | 6 |
Average pore radius μm ≤ | 1.0 | 0.5 |
Thermal CC w/m·k≤ | 5 | 5 |
4. Composite carbon brick
Composite carbon brick’s raw materials are supreme class bauxite, corundum, and graphite, added with special additives. After shaped by static molding, dried, and sintered in high-temperature kiln, composite carbon brick is finally produced. Composite carbon brick is applicable for different volumes of blast furnaces at the parts such as furnace bottom, furnace hearth, tuyere, cinder notch, and so on.
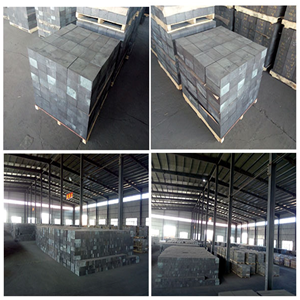
Composite carbon brick characteristics
- Good thermal conductivity.
- Strong iron liquid corrosion resistance.
- Strong alkaline molten slag corrosion resistance.
- Good scouring resistance.
- Long service life, can better protect the furnace hearth.
Composite carbon brick physicochemical index
Item | Index | |
RSCC-1 | RSCC-2 | |
Al2O3 % ≥ | 70 | 75 |
C % ≥ | 9 | 9 |
Bulk Density g/cm3 ≥ | 2.7 | 2.85 |
AP % ≤ | 16 | 15 |
CCS Mpa ≥ | 55 | 60 |
Air permeability mDa ≤ | 1.0 | 0.8 |
Average radium % ≤ | 1 | 1 |
Iron liquid corrosion index % ≤ | 2.0 | 2.0 |
Oxidation rate % ≤ | 1.0 | 1.0 |
Slag corrosion resistance % ≤ | 3 | 2 |
Thermal conductivity(200℃)w/m·k ≥ | 12 | 15 |
Composite carbon brick has both the advantages of traditional ceramic cup brick’s excellent iron liquid corrosion resistance, slag corrosion resistance alkali corrosion resistance, and the advantages of carbon brick’s good thermal stress resistance. Meanwhile, composite carbon brick overcomes the shortcoming of carbon brick’s weak iron liquid corrosion resistance and oxidation resistance. Composite carbon brick almost has all the good high-temperature properties of traditional ceramic cup bricks and avoids each one’s shortcoming. It can significantly prolong the blast furnace’s service life. Lots of application has tested that when composite carbon brick is used in a ceramic cup, blast furnace’s service life can be prolonged more than 7 years. Composite carbon brick can be used at different parts of the blast furnace, especially at the furnace bottom and furnace hearth has important significance for blast furnace’s long service life.