How to Enhance the Strength of Circulating Fluidized Bed Boiler Lining?
The strength of the circulating fluidized bed boiler lining is very important. If the material is not properly selected or the quality control is not done well during the construction process, it is easy to cause large-scale collapse of the castable during operation and even serious wear of the heating surface pipes.
Enhance the Strength of Circulating Fluidized Bed Boiler Lining?
Selection of wear-resistant refractory manufacturers. Since there are many manufacturers of wear-resistant refractory materials on the market, and the quality is uneven, you must pay attention when selecting a manufacturer. It is best to contract the materials, construction and after-sales service to a reputable and qualified manufacturer. In this way, the circulating fluidized bed boiler lining can be guaranteed to the maximum extent. RS Refractory Manufacturer is a powerful refractory manufacturer with rich experience in the production and sales of refractory materials. RS manufacturer has completed many turnkey projects in the design, construction and material supply of circulating fluidized bed boiler refractory lining. If you choose RS manufacturer, RS manufacturer’s products and customer service will not disappoint you.
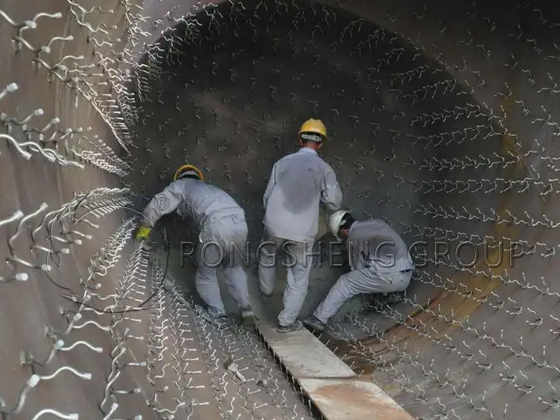
Material selection. Start with the physical and chemical properties of the material (including wear resistance, heat resistance, corrosion resistance, thermal conductivity, stability, thermal expansion, shrinkage, compression and bending resistance and bulk density), while taking into account economy. Combine the characteristics of the lining part, the structure of the components that carry the lining, and the requirements of temperature resistance and wear resistance for comprehensive comparison. Be advanced in technology, reliable in structure and economically reasonable.
CFB lining materials have been developing continuously with the development of boilers towards high parameters, large capacity and new technologies, and many new varieties, new construction methods and technologies have been developed. This has promoted the innovation and improvement of lining structures, continuously improved wear resistance and heat resistance, and promoted the progress of fluidized bed combustion technology. RS manufacturers suggest that accurate design solutions, high-quality material selection, efficient construction quality and maintenance methods can greatly increase the strength of circulating fluidized bed boiler linings.
Why does the Circulating Fluidized Bed Boiler Lining need High-Strength Wear-Resistant Castables?
The main reasons why the circulating fluidized bed boiler lining needs to use high-strength wear-resistant castables are as follows. First of all, the circulating fluidized bed boiler is a high-efficiency, low-pollution boiler with good fuel adaptability, so its operating efficiency and application range have been widely used. However, during the operation of this boiler, due to incomplete combustion of fuel and uneven heat exchange, the temperature and material flow rate in the furnace will be unevenly distributed, causing serious wear and scouring of the boiler lining. Therefore, in order to protect the circulating fluidized bed boiler lining, high-strength wear-resistant castables are needed.
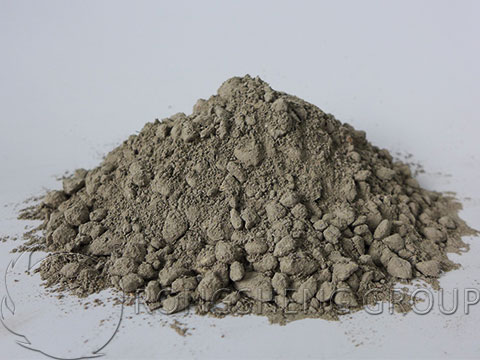
Secondly, high-strength wear-resistant castables are a composite material composed of a variety of polymer materials and wear-resistant materials, with the advantages of high strength, high wear resistance, high temperature resistance, and corrosion resistance. This material can maintain its physical and chemical properties for a long time under a high-temperature environment, and effectively resist high temperature and chemical corrosion in the furnace. In addition, high-strength wear-resistant castables also have good impact resistance and wear resistance, which can effectively resist the high-speed impact and friction of materials and protect the lining from damage.
Finally, the construction of high-strength wear-resistant castables is simple and fast and can be customized according to the shape and size of the boiler, with strong adaptability. This material does not produce harmful gases during the pouring process, which can effectively protect the environment and workers’ health. In addition, the price of high-strength wear-resistant castables is also relatively reasonable, which can effectively reduce the maintenance cost of the boiler.
In summary, the lining of the circulating fluidized bed boiler needs to use high-strength wear-resistant castables to protect it from damage such as incomplete combustion of fuel, material impact and friction, extend its service life, and improve the operating efficiency and application range of the boiler.
Where is the Main Function of Wear-Resistant Castables?
As the name suggests, wear-resistant castables have extremely high wear resistance and can maintain the integrity of the cast body for a long time in harsh working environments. Its wear resistance is better than that of traditional high-aluminum refractory castables, and can extend its service life in key furnace linings. In metallurgy, power and other industries, wear-resistant castables are widely used in rotary kilns, boilers, dust collectors and wear-resistant layers of complex furnace linings, which can effectively resist the erosion of ores, metal materials, high temperatures and chemicals, and improve the operating efficiency of equipment.
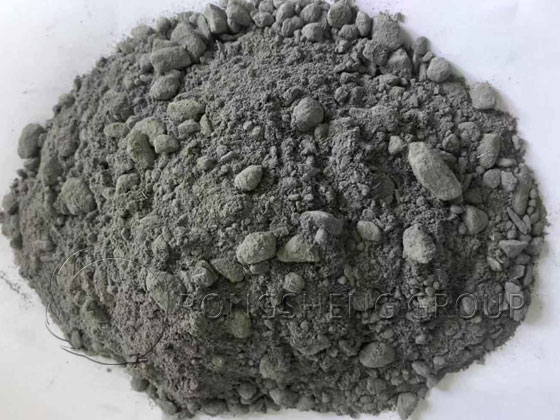
Wear-resistant castables have good corrosion resistance due to the addition of silicon carbide components, which play a skeleton support role and can resist the erosion of various acid and alkali chemicals. In the chemical, petrochemical and other industries, wear-resistant castables are suitable for anti-corrosion layers, which effectively prevent corrosive media from eroding the furnace lining and ensure the stability and safety of the production process.
Wear-resistant refractory castables have high compressive strength and can withstand greater pressure and impact. Moreover, it has good thermal shock resistance, which can reduce the wear and failure rate of the furnace lining, thereby reducing energy consumption and production costs. This helps to reduce the operating costs of enterprises and improve their competitiveness. At the same time, wear-resistant castables also have the characteristics of environmental protection and sustainable development. Their production and use processes meet environmental protection requirements and are conducive to reducing the generation of industrial waste.
In summary, wear-resistant castables play an important role in improving wear resistance, enhancing corrosion resistance, improving compressive strength and reducing energy consumption. It is one of the important refractory castables that are indispensable for industrial kiln linings.