Ceramic Fiber Boards for Energy Efficiency in High-Temperature Applications
In the world of industrial processes, where temperatures often soar to extreme levels, maintaining energy efficiency while ensuring safety is a top priority. High-temperature applications, such as furnaces, kilns, and reactors, demand materials that can withstand intense heat while minimizing energy loss. This is where Insulation Ceramic Fiber Boards come into play, offering an advanced solution for thermal insulation in such demanding environments. These boards not only enhance energy efficiency but also contribute to the longevity and safety of high-temperature systems.
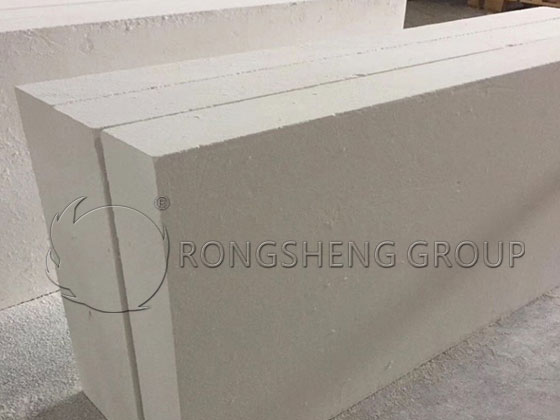
Understanding Ceramic Fiber Boards
Insulation Ceramic Fiber Boards are a type of refractory material designed to provide superior thermal insulation in high-temperature environments. Composed of ceramic fibers, these boards are lightweight yet highly resistant to thermal shock and high temperatures, often withstanding temperatures up to 1600°C (2912°F). Their exceptional insulating properties make them an ideal choice for a wide range of applications, from industrial furnaces to power generation plants.
Ceramic fiber boards are manufactured by forming alumina-silicate fibers into a rigid structure. These fibers are derived from high-purity raw materials, ensuring that the boards maintain their integrity even under extreme conditions. The result is a durable, lightweight, and easy-to-handle insulation material that offers excellent thermal stability and low thermal conductivity.
The Role of Ceramic Fiber Boards in High-Temperature Applications
In industries where high-temperature processes are routine, the need for reliable insulation cannot be overstated. Effective insulation not only helps maintain the desired temperature within a system but also reduces energy consumption, lowers operational costs, and minimizes the environmental impact.
Insulation Ceramic Fiber Boards play a crucial role in achieving these objectives. Here’s how:
Energy Efficiency
One of the primary benefits of using Ceramic Fiber Boards in high-temperature applications is their ability to significantly reduce heat loss. These boards have low thermal conductivity, meaning they are highly effective at blocking the transfer of heat. This property ensures that the heat generated within a system remains where it is needed, reducing the amount of energy required to maintain high temperatures. In turn, this leads to lower fuel consumption and operational costs, making the entire process more energy-efficient.
Thermal Stability
Ceramic Fiber Boards are engineered to withstand extreme temperatures without degrading or losing their insulating properties. This thermal stability is essential for maintaining consistent operating conditions in high-temperature applications. Whether used in a furnace lining, a kiln door, or as a protective barrier in a reactor, these boards ensure that the system operates efficiently and safely, even under prolonged exposure to intense heat.
Resistance to Thermal Shock
In many industrial processes, rapid temperature changes are common, posing a significant challenge for insulation materials. Insulation Ceramic Fiber Boards are designed to resist thermal shock, meaning they can endure sudden temperature fluctuations without cracking or deteriorating. This resistance not only extends the lifespan of the insulation but also helps prevent costly downtime and maintenance.
Lightweight and Easy Installation
Despite their impressive insulating capabilities, Ceramic Fiber Boards are remarkably lightweight. This characteristic makes them easy to handle and install, reducing labor costs and installation time. Their rigidity also allows them to be cut and shaped to fit specific applications, providing a custom insulation solution that meets the unique needs of each system.
Versatility in Application
The versatility of Insulation Ceramic Fiber Boards is another key advantage. These boards can be used in a variety of high-temperature applications across different industries. Common uses include furnace linings, kiln linings, back-up insulation, and as heat shields. They are also employed in power generation, petrochemical, and metallurgical industries, where reliable thermal insulation is essential for operational efficiency and safety.
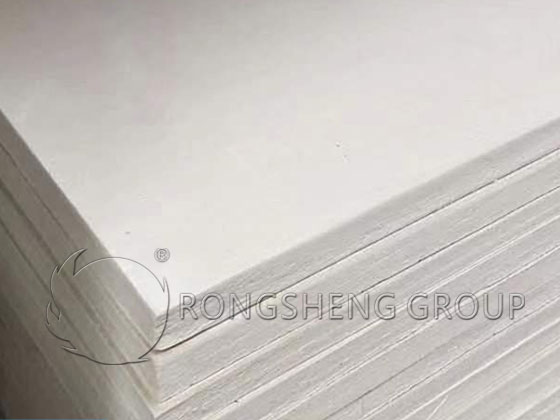
Enhancing Energy Efficiency with Insulation Ceramic Fiber Boards
Energy efficiency is a critical concern in industries that rely on high-temperature processes. The energy required to heat a system to the necessary temperature represents a significant portion of operational costs. By minimizing heat loss, Insulation Ceramic Fiber Boards help reduce the amount of energy required to maintain optimal operating conditions.
Here’s how these boards contribute to energy efficiency:
Reduced Heat Loss
The low thermal conductivity of Ceramic Fiber Boards means that less heat escapes from the system. This reduction in heat loss translates directly into energy savings, as less fuel or electricity is needed to sustain high temperatures. Over time, these savings can be substantial, particularly in energy-intensive industries.
Improved Process Control
Consistent temperature maintenance is crucial for many industrial processes. By providing reliable insulation, Ceramic Fiber Boards help maintain a stable temperature within the system. This consistency improves process control, leading to higher-quality products and more efficient operations.
Extended Equipment Lifespan
High temperatures can take a toll on industrial equipment, leading to wear and tear that shortens the lifespan of critical components. By insulating the system effectively, Ceramic Fiber Boards reduce the thermal stress on equipment, helping to extend its lifespan and reduce the frequency of maintenance and replacements.
Environmental Impact
Energy efficiency is not just about cost savings; it also has a significant environmental impact. By reducing the amount of energy required for high-temperature processes, Ceramic Fiber Boards help lower the carbon footprint of industrial operations. This reduction in energy consumption is particularly important in industries that are striving to meet stringent environmental regulations and reduce their impact on climate change.
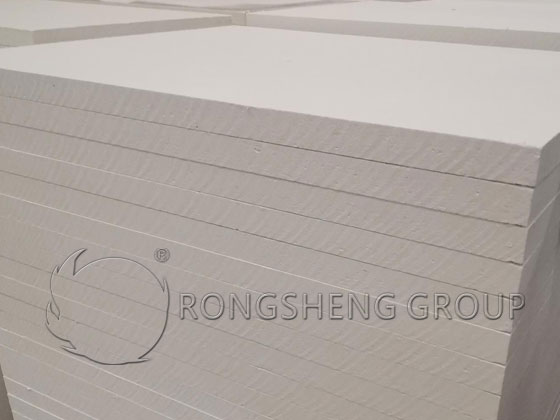
Selecting the Right Insulation Ceramic Fiber Boards
When choosing Insulation Ceramic Fiber Boards for high-temperature applications, it’s essential to consider several factors to ensure optimal performance:
Temperature Rating
Different Ceramic Fiber Boards are rated for different maximum temperatures. It’s crucial to select a board with a temperature rating that matches or exceeds the operating temperature of your application.
Density
The density of the board can affect its insulating properties and mechanical strength. Higher-density boards offer better insulation but may be more rigid and less flexible. The right balance between density and flexibility depends on the specific requirements of your application.
Chemical Compatibility
In some applications, the insulation may be exposed to corrosive chemicals or gases. It’s important to choose a Ceramic Fiber Board that is chemically compatible with the environment in which it will be used.
Installation Requirements
Consider the ease of installation and the ability to customize the boards to fit your application. Some boards are easier to cut and shape than others, which can be an important factor in complex installations.
Exceptional Thermal Insulation of Ceramic Fiber Boards
Insulation Ceramic Fiber Boards are a critical component in optimizing energy efficiency in high-temperature applications. Their exceptional thermal insulation properties, combined with their resistance to thermal shock, ease of installation, and versatility, make them an ideal choice for industries that rely on high-temperature processes. By selecting the right Ceramic Fiber Board for your application, you can enhance the efficiency, safety, and longevity of your operations, while also contributing to a more sustainable and environmentally friendly industrial process. As the demand for energy-efficient solutions continues to grow, Insulation Ceramic Fiber Boards will remain a vital tool in the pursuit of cost-effective and reliable thermal insulation.