High Aluminum Low Cement Refractory Castable Manufacturer
High-aluminum low-cement castable is a castable with a large number of monolithic refractories. That is to say, the addition of calcium aluminate cement is about one-half or one-third of the ordinary cement castable.
Compared with ordinary high-alumina castables, high-alumina, and low-cement castables use ultra-fine powder to reduce the amount of cement and greatly improve the strength and erosiveness of low-cement castables. While increasing the bulk density and reducing the porosity, the service life is increased.

High-alumina and low-cement castables are used in industrial furnaces such as metallurgy, petroleum and petrochemical, electric power, and building materials. A large part has replaced refractory bricks, but as a manufacturer of low-cement castables, we still use different furnace types and temperatures according to users. According to the requirements of different use environments, some high-alumina and low-cement castables with different levels and different body densities are produced. Of course, the prices of different levels, different body densities, and low-cement castables are also different.
The characteristics of high-alumina and low-cement castables are also based on different grades of refractory micro-powder, different grades of main materials, and different grades of bonding agents to determine the quality of the product. In order to facilitate smaller particles, larger specific surface area, and better sintering ability, the castable is more suitable for the working needs of the user’s high-temperature kiln.
In the practical application of low-cement castables, especially in construction, it is also very important to control the amount of water added. Generally, when leaving the factory, the manufacturer will attach the construction instructions for the castable. During construction, it is necessary to strictly follow the construction instructions, and pour and maintain the castable well, so as to exert its maximum effect.
All in all, regardless of production or application, it is necessary to take into account the different effects of temperature, erosion, erosion, etc. on the refractory lining material according to the actual use. Only in this way can the refractory castables used be selected correctly, and with the appropriate construction technology, the service life of the refractory lining can be greatly extended. Save production costs.
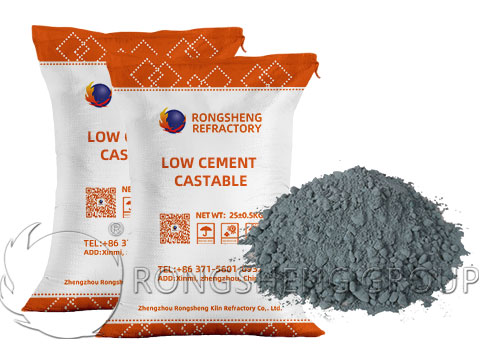
The Difference between LCC Refractory Castable and Ordinary Refractory Castable
Low-cement castables, ultra-low or no-cement castables replace most or all of the cement with superfine powders that have the same or similar chemical composition as the main material. It is formulated by scientifically optimizing particle gradation, micro-powder, particle shape, and other factors, and adding a small amount of dispersant (water reducer) and an appropriate amount of retarder and other compound admixtures.
Compared with ordinary refractory castables, the low cement castable series has many excellent properties.
- (1) Less water consumption. The water consumption of LCC low-cement castables is only 1/2-1/3 (about 5-7%) of ordinary refractory castables. Therefore, the bulk density is high, the porosity is low, and there is no obvious dehydration stage during baking. Good thermal shock performance, comparable to fired products.
- (2) Because the amount of cement is greatly reduced, the high-temperature performance and slag resistance of the material are improved.
- (3) There are few or no hydrates after forming and curing, and there is no hydration bond damage during baking to affect the medium temperature strength. Therefore, no matter at medium temperature or high temperature, its strength does not decrease but increases.
The main application of LCC low cement castable is suitable for petroleum, metallurgy, the chemical industry, and various silicate kilns. Such as some components of the refining device outside the furnace, the cover of the refining ladle outside the furnace, the integral spray gun for molten iron, the treatment of molten steel, and the roof lining of the electric furnace. Soaking furnace, heating furnace, annealing furnace lining, tapping trough. Tundish lining, high-temperature burner, blast furnace tapping ditch cover, ladle lining, etc.
The refractoriness of low-cement refractory castables is greater than 1790°C, and the load softening temperature (4% deformation) at 0.2MPa is 20-100°C higher than that of CA50 cement refractory castables. Therefore, the service temperature of low-cement refractory castables is generally about 100°C higher than that of CA50 cement refractory castables of the same material. The thermal expansion coefficient of low cement refractory castables shows the characteristics of expansion during the whole heating process. It can be seen that as the heating temperature increases, the thermal expansion rate increases, and reaches the highest value at 1250 ° C, which is about 0.68%. Then it began to shrink slowly, and the thermal expansion rate was 0.43% at 1400°C. When the temperature was 1500°C, the thermal expansion rate returned to 0.5%.

LCC Refractory Castable Ultra-Low Cement Castable
Low cement and ultra-low cement refractory castables refer to castable refractory materials with calcium aluminate cement added less than 8%. According to the US ASTM regulations, the CaO content in low-cement castables is required to be less than 2.5%, generally 1.0-2.5. When the CaO content is less than 1%, it becomes an ultra-low cement castable. The materials of low-cement and ultra-low-cement castables include clay, high alumina, mullite, corundum, carbon and silicon carbide, etc. Its ingredients are composed of refractory aggregate, refractory powder, an appropriate amount of superfine powder, an appropriate amount and small amount of calcium aluminate cement (delayed coagulation accelerator), and a trace amount of dispersant (high-efficiency debonding agent). Generally, multi-level ingredients are used, which are divided into 5~3mm, 3-1mm, 1~0.2mm, 0.2~0.074mm, 0.074~0.044mm, and less than 1 micron.

Mullite low-cement castables can be used as inner linings of various high-temperature burners, dressing linings of water-cooled pipes of heating furnaces, etc. Corundum and chromium-containing corundum low-cement refractory castables can be used as the lining of the triangular area of the top of the steelmaking electric arc furnace and the lining of some parts of the refining device outside the molten steel furnace. Such as integral spray gun lining for spray metallurgy, RH and DH vacuum degassing device and dipping tube lining, power frequency induction furnace lining, the high-temperature wear-resistant lining of a petrochemical catalytic cracking reactor, etc.
Al2O3-SiC-C low-cement castables are used as linings for blast furnace tapping troughs, iron furnace tapping troughs, and integral spray guns for molten iron pretreatment.
MgO-Al2O3 or Al2O3-MgO·Al2O3 low-cement castables are used as linings for ladles and tapping troughs.