Castable Refractory for Circulating Fluidized Bed Boiler
There are many types of refractory castables, and the uses of each refractory castable are also different. Such as corundum wear-resistant refractory castables, low-cement refractory castables, lightweight heat-insulating refractory castables, and steel fiber refractory castables. Castables refractory for circulating fluidized bed boilers are mainly high-strength wear-resistant castables. Among them, corundum refractory castable has the characteristics of high strength and good fluidity, which is convenient for construction. It is mainly used for the parts that are easy to be washed and wear, such as the combustion chamber, separator, and flue of a circulating fluidized bed boiler.
Selection of Castable Refractory for Circulating Fluidized Bed Boilers and Precautions for Use
Selection of refractory castables and refractory plastics for circulating fluidized bed boilers. Taking the 75t/h circulating fluidized bed boiler as an example, the main refractory materials used are corundum wear-resistant plastics, diatomite thermal insulation castables, high-strength wear-resistant castables, phosphate refractory castables, lightweight thermal insulation bricks, diatomite thermal insulation bricks, refractory bricks, etc.
Among them, the wear-resistant layer at the lower part of the furnace and the outlet of the furnace are mainly made of corundum wear-resistant plastic. The inlet flue and target area of the separator use high-strength wear-resistant castables. The separator cylinder and cone are made of lightweight thermal insulation bricks, and the surface is made of high-strength wear-resistant castables. Phosphate refractory castables are used for air distribution devices, ignition air ducts, and furnace doors. Diatomite insulation bricks and refractory bricks are mainly used for the heating surfaces of the tail.
Precautions when using refractory castables and refractory plastics for circulating fluidized bed boilers.
- Clean water must be used, and the amount of water added is 6% ~ 8%.
- Use a forced mixer, and all mixing tools must be cleaned. Mix until homogeneous. When stirring, the amount of material added should not be less than the whole package. Dry mix for 15min before adding water to achieve the purpose of mixing evenly.
- The castable is reinforced with a large number of anchoring nails and the metal surface of the boiler. The anchoring nail is a metal material, and the thermal expansion coefficient is much larger than that of the refractory material, so the anchoring nail needs to be preheated before installation.
- The pouring surface of all molds should be coated with a layer of oil.
- Each batch of materials must be poured within 10 to 30 minutes after mixing. It needs to be poured to the specified thickness at one time and then vibrated until it is completely sealed.
- The mold is demolded 24 hours after pouring, and the total curing time is 3 days.
How to remedy the falling off and cracking of castable refractory for circulating fluidized bed boilers?
During the operation of the circulating fluidized bed boiler, some castable refractory for boiler will fall off and crack. This part of the pipe is more prone to wear than other places because most of it occurs in the dense phase area such as the refeeder and below the water cooling screen. When this happens, the usual approach is to repair with refractory castables or plastic refractories. When repairing, the repairing materials should be mixed and stirred first, and then suitable templates and molds should be made at the repaired part. Finally, pour and repair. The repaired material should be basically cured and formed, and then gradually baked according to the heating curve. This repair method is time-consuming, labor-intensive, and quite uneconomical. If it is repaired with blue mud, it can be ignited immediately after construction, which saves time and effort, and is convenient and quick.
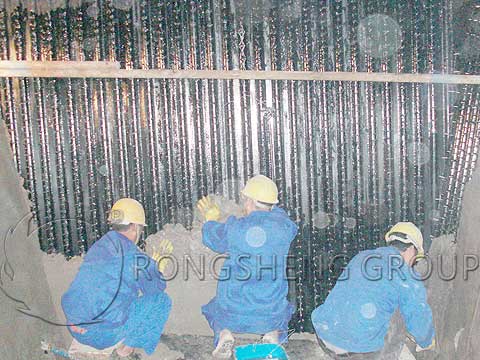
Use special tools to repair the dropped boiler refractory castable to right-angle subsidence of not less than 20 mm, that is, the repair thickness is not less than 20 mm. Clean the repaired area with a brush, slice the blue mud, and stick the new side on the repaired area. Then ram it with a rubber hammer to make it firmly combine with the original refractory castable to form a flat surface.
If the refractory castable falls off and exposes the pin, it can be repaired by cutting it into pieces with blue mud and tamping and compacting. If the drop area is not large, it can be completed in ten minutes before and after. The practice has proved that repairing refractory castables with blue mud is much better than repairing refractory castables with other methods.
What boiler linings are refractory castables generally used for?
The main application scenarios of castable refractory for boilers, power generation boilers, heating boilers, waste incinerators, and other industrial kilns. Specific applications of refractory castables for boilers are as follows.
- Water-cooled wall, cyclone separator, furnace, economizer, water-cooled air chamber, slag removal machine, cold ash bucket, etc. in the power generation industry.
- In the lining of boiler equipment such as civil boilers, biomass boilers, steam boilers, chain furnaces, pulverized coal furnaces, etc.
- Heating furnaces, soaking furnaces, forging furnaces, ladle furnaces, trolley furnaces, etc. in the foundry industry.
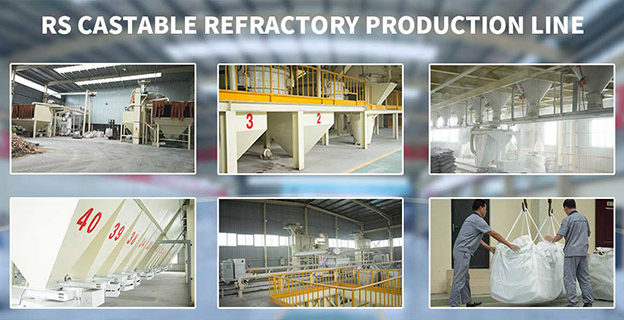
Manufacturers of Refractory Castables for Boilers
Rongsheng refractory material manufacturer, environmentally friendly and advanced automatic unshaped refractory castable production line, with an annual output of tons. Can provide refractory castable lining materials for various industrial boilers. In addition, we can also provide high-quality refractory and wear-resistant plastics, refractory ramming materials, etc. It is matched with the high-quality refractory castable binder produced by Rongsheng, aluminum dihydrogen phosphate. Unshaped refractory lining materials can be formulated with the advantages of strong wear resistance, corrosion resistance, air erosion resistance, high strength, and stable performance. Improve the service life of boiler refractory castable lining. Rongsheng can also design various economical and practical unshaped refractory linings for boiler linings according to the needs of customers and the actual working conditions of boilers. Contact us for free samples and quotes.