Two Different Types of Low Cement Castables
In the refractory castable combined with calcium aluminate cement, the castable with CaO content less than 2.5%, that is, the castable with calcium aluminate cement added about 1/2 to 1/3 of the ordinary calcium aluminate cement castable, It is called low cement castable. Low cement castable materials are clay, high alumina, mullite, corundum, chromium corundum, zircon mullite, zirconium corundum, alumina-spinel, and carbon and silicon carbide, and many more. According to its operating performance, it is divided into vibrating castable and self-flowing castable. Rongsheng refractory manufacturer will introduce the above two different types of low-cement refractory castables for you.
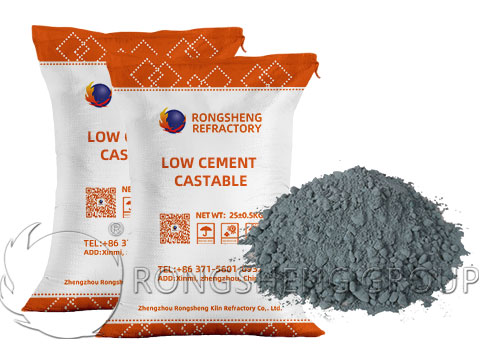
Two Different Types of Low Cement Castable Composition
The ingredients of vibrating low cement castables are generally: refractory aggregate 60% ~ 70%, refractory powder 18% ~ 22%. Calcium aluminate cement 3% to 7% (low cement type) or 1% to 2% (ultra-low cement type). Silica (soot silica) micro powder (or reactive alumina micro powder) 3% ~6%. Trace dispersant. The particle size composition can be according to Andreassen’s particle size distribution equation, and the q value is 0.26 ~ 0.35.
The batching composition of the self-flowing low-cement castable is similar to that of the vibrating low-cement castable, but the particle size composition and fine powder content are different. Generally, the maximum critical particle size of aggregate is not more than 6 mm, and the particle size distribution is in accordance with the Andreassen or Dinger-Funk particle size distribution equation. The value of the particle size distribution coefficient q should be controlled between 0.21 and 0.26, and a larger self-flow value (greater than 180) can be obtained between this value. When the q value is greater than 0.26, the flow value becomes smaller, and it is difficult to cause self-flow. When the q value is less than 0.21, the powder content is too large, which will affect the physical properties of the castable. The content of micro powder (silica micro powder) in the particle size composition is generally 5% ~ 6%. At the same time, high-efficiency dispersants must be used.
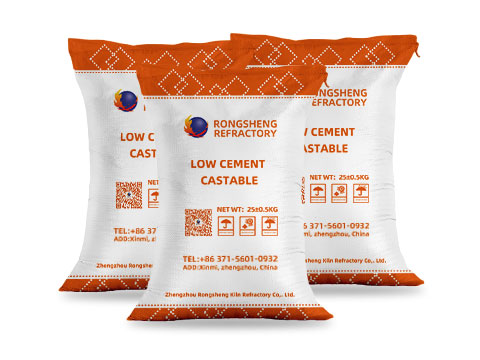
Low Cement Castables Physical and Chemical Indicators
Table 1 shows the typical vibrating low-cement clay, high-aluminum, and corundum casting performance.
Table 1 Vibrating Low-Cement Castables physical and chemical indicators | ||||
Items | Clay Low Cement Castable | High-Alumina Low Cement Castable | Corundum Low Cement Castable | |
w(Al2O3) / % | 45 | 75 | 92 | |
w(SiO2) / % | 50 | 12 | 5 | |
w(CaO) / % | <1.8 | <1.5 | <1.5 | |
Bulk Density / g/cm3 | 110℃, 24h | 2.30 | 2.60 | 3.00 |
1350℃, 3h | 2.26 | 2.61 | 3.10 | |
Compressive Strength / MPa | 110℃, 24h | 72 | 75 | 85 |
1350℃, 3h | 90 | 115 | 125 | |
Linear change rate after burning / % | 1000℃, 3h | -0.3 | -0.2 | -0.2 |
1350℃, 3h | ±0.3 | ±0.5 | ±0.5 | |
Max Use Temperature / ℃ | 1450 | 1600 | 1700 | |
Mixing Water Demand / % | 6.0 ~ 6.5 | 6.0 ~ 6.5 | 4 ~ 5 |
Table 2 shows the general self-flowing low-cement alumina-spinel casting performance.
Table 2 Self-Flowing Low-Cement Alumina-Spinel Castable | ||||
Items | A | B | C | |
w(Al2O3) / % | 90 | 88 | 85 | |
w(MgO) / % | 6 | 6 | 6 | |
w(CaO) / % | 3 | 5 | 8 | |
Bulk Density after Burning / g/cm3 | 110℃, 24h | 3.20 | 3.10 | 3.05 |
1000℃, 3h | 3.10 | 3.08 | 2.92 | |
1600℃, 3h | 3.15 | 2.95 | 2.86 | |
Flexural Strength after Burning / MPa | 110℃, 24h | 6.5 | 9.5 | 10.0 |
1000℃, 3h | 5.5 | 7.6 | 7.8 | |
1600℃, 3h | 30.0 | 21.5 | 20.5 | |
Linear Change Rate after Burning / % | 110℃, 24h | – | – | – |
1000℃, 3h | 0.1 | 0 | 0 | |
1600℃, 3h | -0.1 | +0.8 | +0.9 | |
Amount of Water / % | 4.8 ~ 5.4 | 5.4 ~ 5.8 | 5.5 ~ 6.5 | |
Self-Flow Value / mm | > 185 | > 185 | > 185 |
Low Cement Castable Refractory Material Application
Low cement castable refractory materials have a wide range of applications. In metallurgy, petrochemical, machinery manufacturing, electric power, building materials, and other industrial kilns, such castables have been widely used to replace some traditional fired refractory brick products as linings. Vibration-type low cement castable refractory materials are mainly used as thick-sized linings. Such as heating furnace, various heat treatment furnace electric furnace cover shaft kiln, rotary kiln, blast furnace tapping channel, ladle, hot metal ladle, etc. The self-flowing low cement refractory castables are mainly used as thin linings and linings for high-temperature refractory components with metal anchors. Such as the outer lining of the water-cooled pipe of the heating furnace, the lining of the integral spray gun for jet metallurgy, the lining of the immersion pipe of the RH and DH vacuum degassing device, and the air supply element of the ladle (breathable brick). And the high-temperature wear-resistant lining of the petrochemical catalytic cracking reactor.
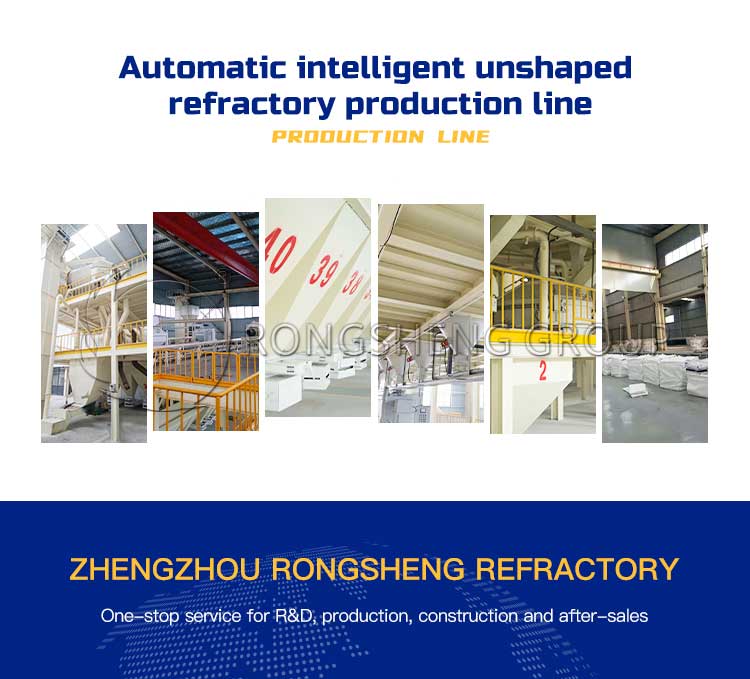
Refractory Castables Manufacturers
As one of the refractory castables, the unique advantages of low cement castables play an important role in refractory lining materials. Rongsheng refractory castable manufacturers have rich experience in production and sales. Its advanced environment-friendly and fully automatic unshaped refractory castable production line have an annual output of 80,000 tons. To provide our customers in more than 60 countries with high-quality refractory lining materials. For example, Russia, South Africa, Kazakhstan, Philippines, Chile, Malaysia, Uzbekistan, Indonesia, Vietnam, Kuwait, Turkey, Zambia, Peru, Mexico, Qatar, etc. Rongsheng used to customize low cement castables for customers, ultra-low cement castable, and high customer return rate. To obtain free refractory lining material configuration solutions for high-temperature kilns and solve difficult refractory lining material problems, please contact us. We will customize the refractory lining scheme for you according to your actual production situation.