The Influence of Certain Oxides on the Performance of Magnesia Chrome Bricks
In the production process of magnesia chrome bricks, there will be a variety of additives. For example, chromium oxide, aluminum oxide, zirconium oxide, iron oxide, etc. These additives have a very important influence on the performance of magnesia chrome bricks. The Rongsheng refractory manufacturer will make the following specific analysis on the influence of these four oxides on magnesia-chrome bricks.
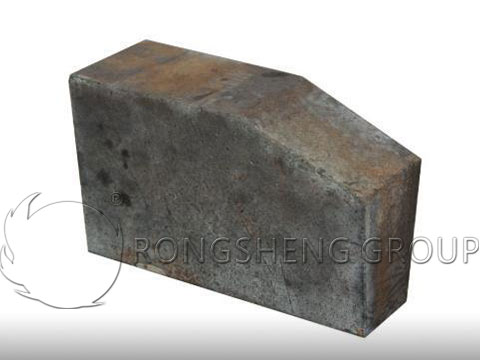
The Influence of Chromium Oxide on Magnesia Chrome Refractories
Chromium oxide is one of the main components of magnesia-chromium refractories. Appropriate addition of chromium oxide components with high purity and small particle size to magnesia-chromium refractories has the following three main effects on magnesia-chromium refractories.
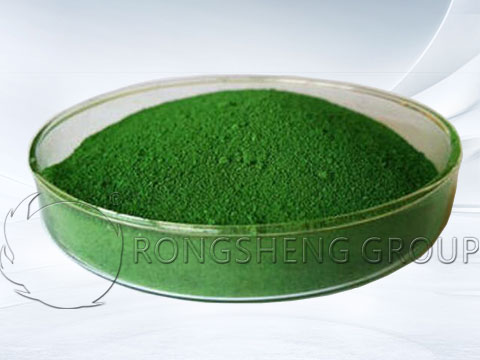
(1) Increase the direct binding rate
When the content of Cr203 in periclase increases, the dihedral angle between silicate melt and periclase increases. This principle also leads to poor wettability between silicate and magnesia-chromium spinel compared to silicate and magnesia-iron spinel. This phenomenon also causes the silicate to be distributed only in the form of islands between the magnesia-chromium spinels, and the direct bonding in the magnesia chrome bricks body increases.
(2) Improve strength
During the sintering process, the periclase solid solution in the magnesia-chromium refractory material has the dissolution and re-dissolution of spinel during the re-dissolution of silicate. Because of their similar crystal structure, spinel can form a large amount of secondary spinel around the periclase crystal, which improves the strength of the product and the slag resistance. The addition of high-purity small particles of chromium oxide to the magnesia chrome brick can promote the formation of spinel and promote the formation of secondary spinel.
(3) Increase slag viscosity
When the magnesia-chromium refractory contains more chromium oxide components, due to the low chemical activity of the chromium oxide components when chromium oxide is present in the slag, the viscosity of the slag component increases.
The Influence of Alumina on Magnesia Chrome Refractory Bricks
The addition of alumina to magnesia chrome refractory bricks has different effects depending on the raw materials used. The raw materials contain more impurity components such as CaO and SiO2. The addition of appropriate alumina components can promote the sintering of magnesia chrome refractory bricks, and the brick structure will become denser. This is because alumina can form low-melting substances with calcium silicon and other components in the refractory bricks. The formation of these low-melting substances accelerates the sintering and densification process.
However, due to the different content of CaO and SiO2 in the raw materials, the influence of the crystal structure of periclase and other crystalline materials in the raw materials causes differences in the content and diffusion of CaO and SiO2 in the brick body. When the amount of CaO and SiO2 diffused to the boundary is not enough to meet the reaction rate of alumina, the remaining alumina will react with MgO in the periclase crystals. The reaction equation is as follows:
MgO+Al2O3=MgO·Al2O3
That is, spinel is generated at the grain boundary and other positions in the brick body, and the volume and density of the magnesia-aluminum spinel, which is the reaction product of MgO and Al2O3, is quite different. Therefore, this reaction is accompanied by a larger volume expansion. This hinders the sintering reaction of the magnesia-chrome brick body to a large extent, which increases the pores in the brick body and reduces the strength.
In other words, to add alumina to the magnesia-chromium refractory bricks, it is necessary to consider the CaO and SiO2 components in the raw material, and appropriately add alumina. If most of Al2O3 is added, it can react with the silicon-calcium component in the brick body to form a low melting phase, and it can present a continuous distribution in the brick body. At this time, due to the increase in the amount of liquid phase during the sintering process, it can promote the material transfer during the sintering process, promote the sintering of the brick body, and increase the density of the product. On the contrary, if the content of CaO and SiO2 is too low, it is not enough to meet the conditions of consuming Al2O3 to generate the liquid phase. Because the Al2O3 at this time will react with the MgO component in the brick body to form a spinel. The volume expansion caused by the formation of spinel cannot be well alleviated, the density of magnesia chrome bricks products will be reduced, and the compressive strength at room temperature will be affected.
The Influence of Zirconia on Magnesia-Chromium Refractory Materials
The addition of zirconia can improve the performance of magnesia-chromium refractory materials to a certain extent.
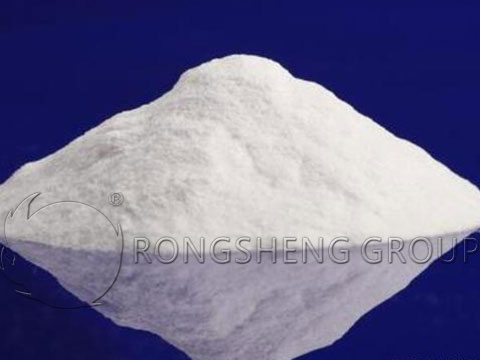
(1) ZrO2 has strong chemical stability. It shows good chemical inertness to general glass melts and acids and bases and is not easy to be wetted by metal solutions.
(2) ZrO2 can change the aggregation state and grain shape of the crystal grain boundary phases in the magnesia-chrome refractory materials, and reduce the dihedral angle between the crystals, and promote the bonding between the crystals.
However, the addition of too much ZrO2 is detrimental to magnesia chrome refractory materials. This is because ZrO2 has a small solid solubility in magnesium oxide. If an excessive amount of ZrO2 is added, the residual ZrO2 will remain between the crystal grains, hindering the mass transfer during sintering, and is not conducive to the densification of the brick body.
The Influence of Iron Oxide on Magnesia Chrome Bricks
Due to the presence of magnesia-iron spinel, iron oxide can promote the sintering of magnesia chrome bricks to a certain extent. However, due to the valence of iron oxides, the solid solubility of the two oxides FeO and Fe2O3 in periclase is slightly different. For this reason, magnesium-chromium products with high iron oxide content are not suitable for copper smelting production with an unstable atmosphere and unstable temperature.
If a magnesia chrome brick with higher iron content is used in a copper converter, it may generate a bulging and loose layer due to the following phenomena. In the case of high-temperature reduction, Fe2O3 in the periclase solid solution will be reduced to FeO and low-iron spinel in the brick body. In the lower temperature or oxidizing atmosphere, the low-iron spinel will be oxidized again to generate MgOFe2O3. In this process, the volume changes, which will cause the explosion of magnesia chrome refractory and the formation of evacuation layers.
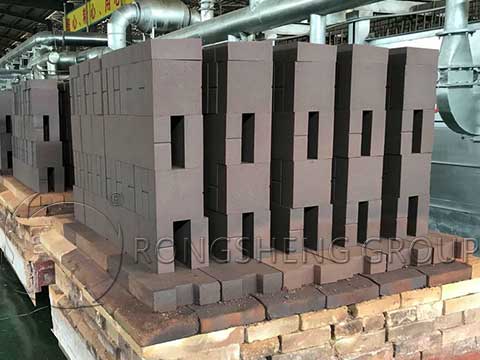
The above-mentioned substances have not only their own influence on magnesia chrome refractory materials during the use of the copper smelting process. Its interaction with iron-silicon slag and SO2 atmosphere is also worth noting.