Magnesia bricks are usually called sintered magnesia bricks, are kind of basic fire bricks with the largest output and widest applications. According to the MgO content, magnesia bricks can be divided into 3 grades: 90, 95 and 98. The corresponding minimum MgO content is 86%, 91% and 96%. By production craft, magnesia bricks can also be divided into burned magnesia brick, unburned magnesia brick, fused re-bonded magnesia brick and chemically re-bonded magnesia brick.
RS Refractory notes that, the production flow of sintered magnesia brick are: magnesia sand → grinding → dosing → mixing → molding → drying → sintering → selecting → packing.
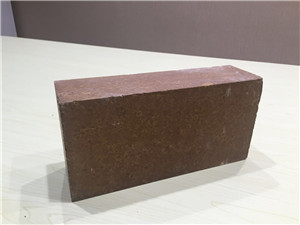
Magnesia Bricks Characteristics
Magnesia bricks have a refractoriness of over 2000℃. But refractoriness under load temperature of MgO bricks varies hugely with the melting point of cementation facies and the quantity of high temperature liquid phase. The rupture under load temperature of ordinary magnesia brick begins at 1520~1600℃, while the high purity magnesia brick can reach to 1800℃.
Thermal conductivity rate of magnesia brick is very high, only lower than carbon bricks. Magnesia brick can resist ferric oxide containing and calcia containing basic slag corrosion, but can’t resist silica containing acid slag corrosion. So, magnesia bricks should not directly contact with silica bricks during using, and should be separated by neutral bricks.
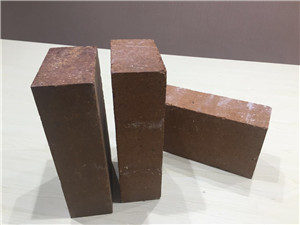
Magnesia Bricks Properties
Item | SMZ-89 | SMZ-91 | SMZ-93 | SMZ-95 |
MgO %≥ | 89 | 91 | 93 | 95 |
SiO2 %≤ | / | / | 3.5 | 2.0 |
CaO % ≤ | 3.0 | 3.0 | 2.0 | 2.0 |
Apparent porosity %≤ | 20 | 18 | 18 | 18 |
Cold Crushing Stength Mpa≥ | 50 | 60 | 60 | 60 |
Refractoriness under load ℃≥ | 1550 | 1560 | 1620 | 1650 |
Permanent linear change (1650℃, 2h) % | -0.6~0 | -0.5~0 | -0.4~0 | -0.3~0 |
Thermal conductivity coefficient (1000℃)(w/m.K) ≤ | / | 3 | / | 3.8 |
Magnesia Bricks Applications
Magnesia bricks have good high temperature performance and strong metallurgical slag corrosion resistance. So magnesia bricks are widely used in steel smelting furnace lining, iron alloy furnace, iron mixing furnace of steel industry, nonferrous metals smelting furnaces linings such as copper, lead, stannum, zinc and so on. Magnesia bricks are also used in lime calcining kiln, glass kiln regenerative chamber checker, high temperature sintering kiln, such as magnesia sand sintering high temperature vertical kiln, basic bricks sintering high temperature tunnel kilns, etc.
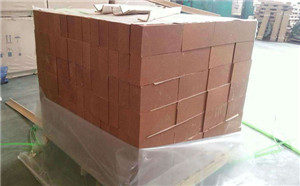
RS Kin Refractory Factory
For the selection of the Refractory Material, RS Kiln Refractory Factory, can not only provide research & develop, as well as sales of monolithic and shaped refractory materials. For the last 20 years, RS Factory has provided numerous refractory materials products and technical service for customers in Southeast Asia, Africa, Europe and North America. RS Refractory main products include all kinds of refractory bricks, castable refractory, refractory cement & concrete, ceramic fiber material, graphite electrodes and so on, are widely used in iron and steel, nonferrous metal smelting, chemical industry, electric power industry, machinery, and other industries.
If you have furnaces are in need of the refractory materials, Please contact RS. You are always be welcomed to RS Factory, And we are looking forward to cooperation with you.