AC Electric Furnace Bottom Refractory Material Description
AC electric arc furnace bottom was primarily constructed by pitch & tar bind magnesia ramming mass or brine magnesia sand. Brine magnesia ramming mass has poor erosion resistance, can’t meet using requirement. Although pitch tar immersed magnesia ramming mass has better durability, its workability is not good, meanwhile, it will pollute environment. Afterwards, magnesia bricks and low grade magnesia carbon bricks are popularly used for the masonry of furnace bottom. But the masonry of magnesia bricks and magnesia carbon bricks is labor consuming and time consuming. Sometimes, if the masonry can’t meet using standard, production will be ceased. So dry ramming mass is gradually used for the built of furnace bottom.
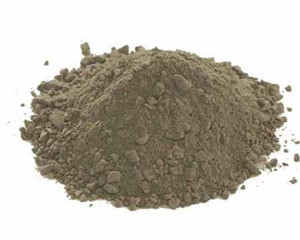
Dry ramming mass is simple and convenient for construction, don’t need to heat after construction and can directly smelt steel. The most often used dry ramming mass is MgO-CaO-Fe dry vibration ramming mass. Because of low melting point calcium ferrite in it, magnesia calcia iron dry vibration ramming mass can quickly get sintering mechanical strength when temperature raises to 1200℃. It will also occur sintering shrinkage under steel liquid’s hydraulic pressure, bulk density can increase to 3.0g/cm3. So MgO-CaO-Fe dry vibration mass has excellent erosion resistance and has excellent using performance. Refractory material consumption declines from 4~8kg( pitch immersed magnesia brick bottom) to less than 2kg/ton steel.
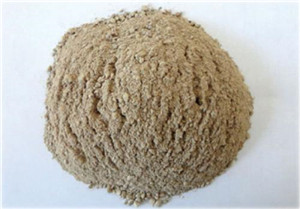
Furnace Bottom Refractory Material Physiochemical Index
Item | Pitch bind magnesia bricks | Pitch magnesia ramming mass | Air permeable dry magnesia calcia ramming mass | Magnesia brick | Magnesia carbon bricks |
MgO % | 90 | 90 | 75.5 | 97 | 80 |
CaO % | 2 | 3 | 20 | 1.8 | 1.5 |
Fe2O3 % | 1.5 | <2 | 3.5 | / | / |
SiO2 % | <4 | <4 | 1.5 | 1.5 | 1.5 |
C % | 5 | 7 | / | / | 14 |
Bulk density g/cm3 | 2.9 | 2.50 | 2.40 | 3.02 | 2.95 |
Apparent porosity % | <7 | / | / | 16 | <5 |
Compression strength Mpa > | >40 | >30 | / | >30 | >30 |
Max. working temperature | 1750℃ | 1700℃ | / | / | / |
Some modern electric arc furnace’s per ton steel dry vibration ramming mass consumption is less than 0.3kg. It is due to steel smelting craft, during using, dry ramming mass will be gradually sintered, ramming mass closes to steel liquid is sintered and densified, then is transition layer, and next is loose un-sintered layer. Un-sintered layer has low density, low thermal conductivity rate, which is very important for heat insulating and energy preservation of electric arc furnace.
Construction quality and working conditions are crucial for the service life of dry furnace bottom ramming mass. It is also called dry vibration castable. As vibration density of this material is more than 0.2g/cm3 higher than ramming method, which will significantly enhance erosion resistance. So this kind of dry refractory material should be constructed by vibration method, especially for AD electric furnace bottom which is not convenient for hot patching.